The convergence – IT, OT, and management working together
Rarely does an opportunity come around in the industry for all aspects of the organization to come together for everyone’s benefit. Industry 4.0 allows that to happen. The digitalization of industry can benefit all aspects, allowing the business to make better decisions around schedule, price, and volume and providing operations with better tools to make decisions about maintenance, downtime, and upgrades of equipment within a plant or factory.
Evolving toward IoT and Industry 4.0 allows for many things to occur. Maintenance cycles can be improved, which positively affects planning and production. The roadmap toward the continuous improvement in your maintenance approach outlined in Figure 1.3 provides an idea of how your outlook and planning can be improved over time.
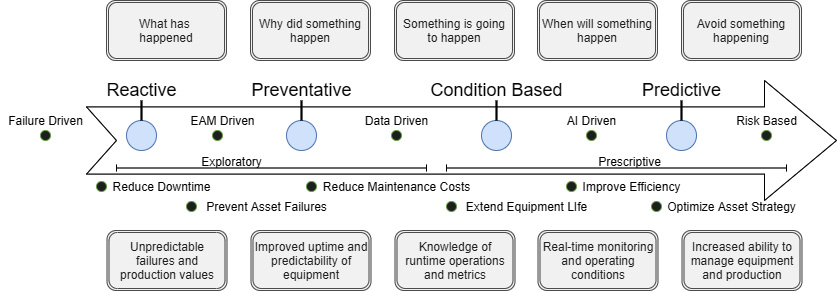
Figure 1.3 – Driving toward common operational goals
This is not an overnight process to achieve results with instrumentation and monitoring improvements, so we wanted to talk about the progression and the maturity curve that might be adopted moving forward.
Reactive and preventative maintenance
Many companies are in the first two categories of reactive or preventative maintenance.
Reactive maintenance is where we basically run our equipment until it breaks. When a piece of equipment or production line breaks, or when we notice some issues with the machine, then we fix it. For example, we replace the belt when it breaks. This is fine in some cases where the fix is simple and relatively inexpensive, but if we need to order parts or the replacement effort is extensive, it could result in unexpected downtime and poor production results if the break is in the middle of an important production cycle.
Preventative maintenance is a little better. It’s often driven by the calendar or perhaps usage-based (number of hours), similar to changing the oil in your car every few thousand miles. It may be driven by an enterprise asset management tool that is put in place to manage inventory and track and manage assets based on tickets from the field or by using the provided manufacturer guidelines for scheduling maintenance. So, for our previous example, the belt is scheduled to be replaced every few thousand hours based on the manufacturer’s recommendation.
The advantage of preventative maintenance is that downtime can be better scheduled, and unexpected downtime can be reduced. It may be the best you can achieve with in-depth instrumentation; however, it may not be enough. One concern is that you may over-maintain your assets or under-maintain them, which can cost you more in maintenance or asset replacement costs.
Even as we move further down the optimization chain, I don’t think we will ever really replace these types of maintenance. Things happen, and reactive maintenance is necessary. And yes, that belt should be replaced on the recommended schedule. Production machinery almost always needs constant love and care. But the long-term benefit is that you don’t have to devote attention to it as if you were in the Army, where if you are not training or sleeping, you are performing preventative maintenance on your vehicles, weapons, whatever, whether it is needed or not. Of course, in this case, the ultimate goal is to keep you alive, so not a bad thing in context.
Condition-based maintenance
As we start to initialize data and collect more information from the individual assets, we can move to condition-based maintenance. We can look closer at the real-time conditions around that asset. Measurements such as current output combined with solar conditions or compared with other solar modules can help us understand whether a component is underperforming and may need to be looked at more closely.
With condition-based maintenance, we get into the habit of not performing maintenance too early or too late but in line with actual data from the equipment and its performance.
Predictive maintenance
Predictive or prescriptive maintenance takes this one step further by adding machine learning modeling to remove the human component from the monitoring process and provide feedback based on what it has learned about optimum operating conditions. Some would argue that these are two different things.
Predictive maintenance helps to forecast potential problems or outcomes with your environment. Prescriptive maintenance helps to provide recommendations based on those outcomes. Neither of these is new to us. Consider the wayfinding application on your phone, which tells you in advance of a delay ahead on your route. Many of these applications will prescribe alternate routes and determine the time savings or delay.
Eventually, some companies may lean into risk-based maintenance, which helps you consider the risk that this part will fail. How will production be affected? Or what downtime may occur if it does fail? Essentially, what is my cost if I keep running and a failure does occur?
Approach with caution
We have all seen or heard of the don’t-touch-it mentality from production teams who just need to keep their system running. When systems are old, decades old, there can be a lot of lost knowledge about how those systems work. Parts may be hard to replace, and sometimes, things work that shouldn’t. These are some of the challenges that operations teams face, and it can be hard for anyone outside those teams who need to get a better look at what is happening inside.
These types of environments and equipment need to be approached with an abundance of caution. Trust is a big factor, and sometimes IT needs to earn trust and not come in like a knight on a white horse, suggesting it will fix all the problems of the day. Everyone in the organization needs and wants progress, from the boardroom all the way to the equipment operator on the shop floor. However, moving too fast in some challenging environments is the easiest way to lose trust within the organization.
We have found from experience in many different industries that most operators love to share information about how they do their job, how they treat their equipment, and, mostly, how things could be made better. Having worked in consulting for many years, it is incredible what you can learn when you talk to subject matter experts in the field, learning everything from farming to fracking, with experts always being generous with their time when approached respectfully. Here are a few simple steps as an approach to this. Some of these tactics seem almost silly to say out loud, but they’re essential to keep in mind:
- Listen and learn: Understand what all the stakeholders know about a system and how it works. What are their concerns, big and small, and what suggestions can they provide for improvement moving forward?
- Define success: Understand what success means, whether this is for one piece of equipment, an entire line, or the plant. Knowing your end goal can help you stay focused and on track.
- Research and share: Learn more about the options you may have for instrumentation and sensor deployment. Share what you have learned with the operators and discuss the pros and cons. Do not get fixated on a single path until you find some general consensus on what could work. Even if you know you are right, it won’t hurt to bring everyone along with you through consensus building.
- Proceed with caution: Finger-pointing when something goes wrong can be a disaster, not only for the people involved but for the project as a whole.
Sending up trial balloons (or conducting a spike in the agile world) for testing can be a viable approach. Testing out different sensors or interfaces without full commitment will allow you to evaluate the pros and cons of the approach and share the results with stakeholders.
Of course, all these guidelines are focused on production equipment, when a mistake is liable to cause serious problems through equipment downtime or worse. A standalone temperature sensor doesn’t require nearly as much effort, but it’s probably not wise to grab the first one you see and run with it. Even low-impact sensors should be evaluated against some of the guidelines discussed earlier. We outlined some considerations when sourcing equipment and sensors, but we have not addressed the approach for determining whether the sensor can provide the correct measurements. Ensure that you discuss equipment tolerances, temperature fluctuations, and pressure and vibration values. This allows you to choose sensors that can operate within the machine tolerances and provide measurements at the right frequency.