The six core practices of Kanban
Beside the four principles there are six core practices to follow when using Kanban; stick to these six and you will be on your way to get a streamlined Lean system that works effectively. Kanban works on a personal as well as on an organizational level and both on big and small companies.
Practice 1 – visualizing your work
The first practice is to visualize what you are doing. This includes both the steps in the process and what work you currently have in each step.
You can use an electronic board or a physical whiteboard. It's great to have an electronic tool but so far I haven't seen anything that beats a big whiteboard. A whiteboard, because of its size, will easily give you an overview of the status and it´s flexible; you just draw new lines and add text wherever it's needed. The whole team can stand around it, get a good understanding about a project or process, and they can update the status simultaneously. If you can get a whiteboard on wheels, you can take it with you when you are in meeting rooms. The following image shows you how your whiteboard may look, with each column signifying a step in the process and the cards indicating the work you have to do in each.
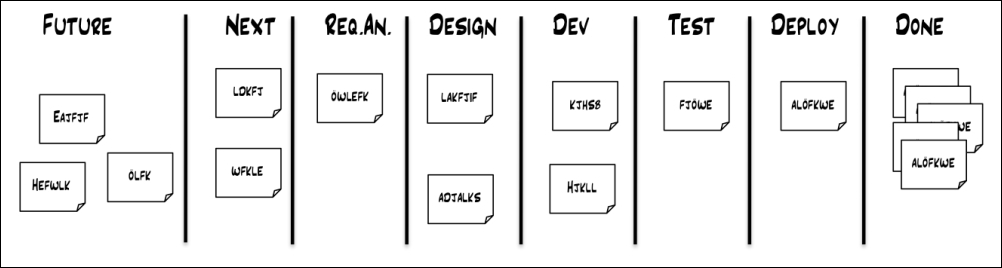
Process steps and work shown on a Kanban Board. In this example it starts with an unsorted queue for future tasks followed by the sorted queue for the tasks to undertake next. The following process steps are one each for analyzing the requirements, designing the software architecture (design), development, testing, and deployment. At the end is a column for tasks that are done.
Practice 2 – limiting work in progress
The second practice is about limiting work in progress, also called WiP. By setting limits, you are not allowed to bring more work in than you are able to handle. If the persons working in the earlier process step work faster than the ones in the next step, then the work stays in the column until there is available capacity in the next step and they are ready to bring it in. Because of rule 2, the earlier steps are not allowed to bring more things in than what its limit allows. This is to prevent you from building queues of half-done work inside the system. Piles of unfinished work are one of the biggest wastes according to the Lean philosophy. What are people that are working in the early steps to do if they have reached the limit and are not allowed to bring more work in? Either they do nothing or even better, they check what they can do to help the bottleneck.
The following image shows the same Kanban Board when you have added limits:
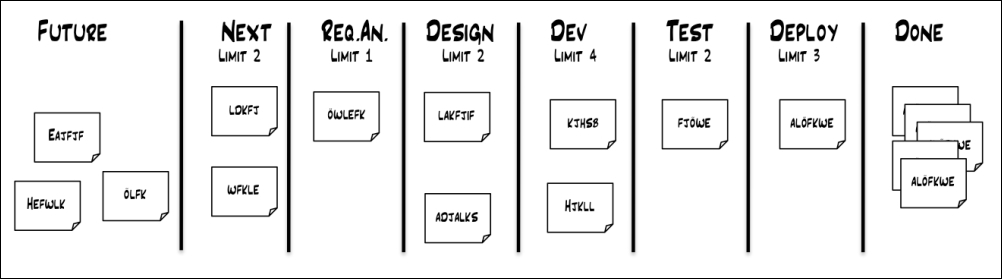
Process steps, work, and limits shown on a Kanban Board. If requirement analysts, who have a limit of 1, are done then they can't bring more work in since the next step, the design step, has reached its limit of 2. The only way for requirement analysts to get an empty slot is when designers have available slots.
In the example, you can see that the process steps Next, Requirement analysis, and Design have reached their limit. It might be that the Design step is the bottleneck and that the people working with requirement analysis are doing nothing. We don't know that by just looking at the Kanban board but we do know that they are not allowed to start working on something new.
Practice 3 – managing flow
The third practice is about improving the flow of a process so the time-to-market, also called lead-time, is decreased.
This image describes the lead-time for an item.
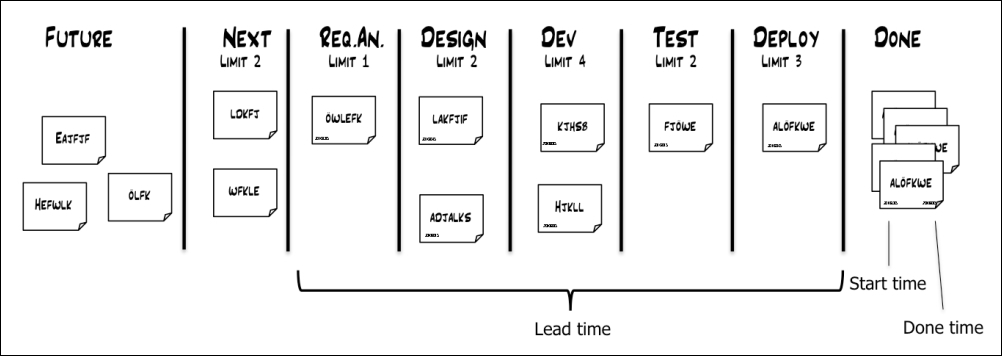
Lead-time is the time from when we start working on an item until we are done with it
The lead-time could be measured in many different ways. In the previous example, the lead-time is from when we start working on the item until we have deployed it. It would also make sense to measure the time from when the item was requested until it was deployed. In the diagram this would be when the item gets into the list named FUTURE.
Since the third practice tells us to optimize the lead-time, here is where we start changing organizations and the way they work. This is not simply because a selected process tells us to, but because we believe the change will decrease the lead-time. Our belief is that the organization is more willing to change when they know why.
The value of the requested product is likely to decrease over time and that's the reason for the third practice. We don´t want it to take too long a time from the request until we deploy the product.
Practice 4 – making process policies explicit
The fourth practice is about being clear about the process and the policies and principles behind it. This is to make sure everybody involved knows and follows the process and can suggest improvements of it. The reason is simply that it's very hard to discuss and improve a process unless you know what the current process is.
Practice 5 – implementing feedback loops
According to practice 3, you should measure and optimize the lead time and this will help you become successful. But wait a minute, just delivering fast is not everything; delivering the right things is also important. To know this you need to know what the customers, the end users think, and how well the product contributes to your company's revenue and wellbeing. Here is where practice number 5 comes into the picture, the need for getting feedback from people outside of your system. There is also a need for feedback loops within a system to make sure you deliver the expected functionality with the right quality. Here is where different kinds of tests come into the picture. Automated tests that run continuously are preferred since they make feedback loops shorter.
Practice 6 – improving collaboratively, evolving experimentally (using models and the scientific method)
The sixth practice is the one that makes Kanban more interesting, as well as more complicated. This practice tells us to use all theories about flow you can find and apply it to your process in order to fulfil practice number three (optimizing lead-time). These theories can be Lean, queuing theory, chaos theory, gaming theory, theory of constraints, and probably many more. This will take a while to learn, but it will be worth it in the long run. The practice also tells us to take decision of changes in consensus to make sure everyone is aligned with the decision.