Analyzing the elements of automation – components and structures
Viewing automation in terms of its components can be linked to the study of the morphology of living things. These components, at a broad level, are the controller, sensors, and actuators.
A machine is a mix of mechanics, mechatronics, electricals, and electronic components. The mechanical components are the gears, conveyors, structure, safety guards, base or foundation, hydraulics, or pneumatic connection. The electrical installations usually cover the electrical panels where all the electricals and electronics are mounted, such as the cabling and power connection. The electronics are components such as the programmable logic controller (PLC), human-machine interface (HMI), drives, motors, input/output (I/O) modules, sensors, actuators, and programming software. All these together form the machine. Without even a single element, the machine will fail to operate. Each element needs detailed attention, and this is the way any machine is built, developed, and then commissioned on any factory floor. The traditional approach to machine building involves building mechanical components as it is the most time-consuming and resource-intensive activity. Once the mechanical element is nearing completion, the electrical cabinet manufacturing and cabling can be started as it is the next most time- and resource-intensive work. After this, the software can be developed, installed, and tested to check the entire machine. However, with various advancements such as digital twins, the simulation of the electrical and software development can start in parallel, helping machine builders achieve a reduced time to market.
Control, automation, and data technologies
Automation forms a part of Industry 3.0, and can also be called digitization. Data technologies, which are the backbone of Industry 4.0, provide the means to monitor and assist managers to make competent decisions, based on events and measurements from the shop floor.
Control is the design effort to keep a chosen parameter within defined limits, even as the process environment changes. Control predates digitization and even electronic controls. Automation is a means of defining in great detail a control process and a means to perform the control task tirelessly and repeatedly according to the programming.
Automation is not technically a necessary element for data technologies. Yet, if the elementary parameters of throughput and quality are not achieved using good control automation, the benefits of data techniques cannot be obtained.
Now, let us understand the control loop. There are three standard parameters in a control loop. There is, first and foremost, the parameter to be controlled; it is called the control variable. It could be the level of liquid in a tank, the temperature of a substance, or something along similar lines. Next, there is a set point. This is the desired value to be attained or maintained by the control variable. There will be a measurement of the actual value of the control variable—what its value is now. The difference between the set point and control value is the deviation, usually called the delta, which is the third parameter. This deviation will act on a control element—a valve or a heater or something—to reduce this deviation. We will explore many control schemes. In every chapter, we will take objects that you encounter in everyday life. We will touch briefly on some of the processes involved in the manufacturing of these items. We will sketch out the control schemes employed to improve productivity in this manufacture. We will give some hints as a starting point for faculty and students to devise experiments in controls using automation:
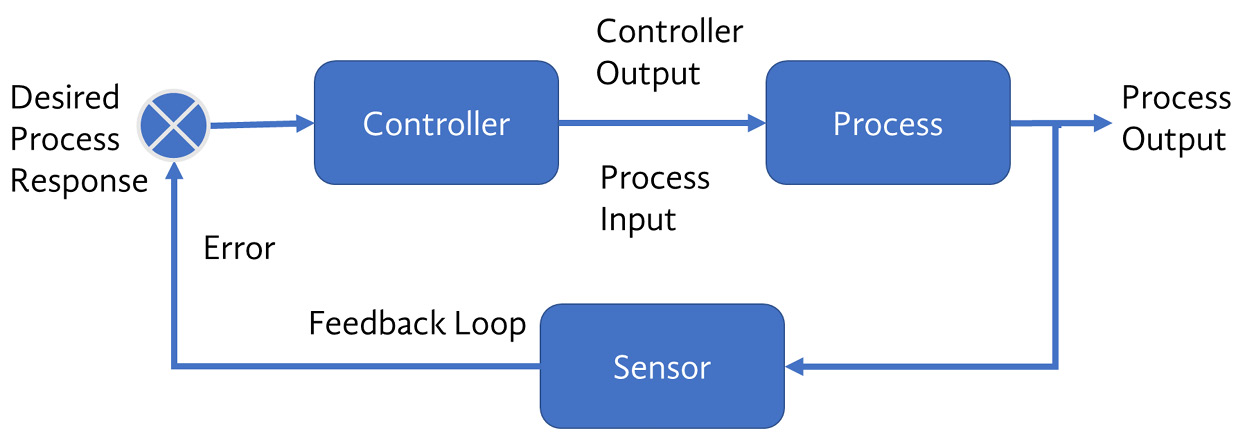
Figure 1.7 – A typical closed-loop system in industrial automation
An efficient control algorithm is one that keeps the process variable (PV) within permitted limits around the set point. The greaterore the number of excursions, the higher the amplitude of the excursions, and the worse the algorithm is. Some of the factors that influence the behavior of a control algorithm are the inertia of the load system, noise in measurement, the frequency of sampling of the control variable, the rate of change of the process variable (for example, jerk change), and the rate of execution of the control program itself.
Control algorithms and PLC programs
A PLC program is a representation of the control algorithm in software. A typical PLC program cycle works like this: initially, all inputs are scanned and recorded in the local memory. This constitutes the input image and is assumed consistent; that is, all values have the same timestamp. Then the logic is executed, and outputs are calculated and written to the output image. Finally, the output image is transferred to the actuators. Hence you can see that there is, in the worst case, a latency of three cycle times. The discussion becomes more complex if you consider remote I/O systems, multiple controllers communicating on a bus, and what is very common—control loops inside control loops. The inertia of the load is not always mechanical inertia in moving parts. It is sometimes, for example, thermal inertia, such as when you try to heat an object, depending on its heat capacity, the response (increase in temperature) can be slow. The control algorithm needs to have this inertia and the latencies as factors. Control algorithms need tuning for a given installation. This is mostly a manual input and is provided by experienced operators. Present-day practice is moving toward auto-tuning to increase operator comfort. A practical issue is that during tuning, the material is wasted. Hence, the need arises to shorten the time needed for tuning and the trial-and-error involved so that wastage is minimized.
We are primarily going to examine automation in the field of manufacturing; therefore, we always talk of industrial automation. Thereby, we distinguish it from office automation—by which we refer to the hardware and software used for the automation of office functions, such as accounts, HR, sales, and inventory. In this book, we will walk our way through using control algorithms as our street guide and understand them by exploring how they play a role in making some of the very familiar products we use daily. This structure allows us to have a good idea of the progress achieved as we go along. The idea is that some control problems are common to the manufacturing of many products, and at the same time, any product will use many control elements. It is also very interesting that the same control problem is solved using different control elements, different control algorithms, and, particularly, different control strategies. Industrial automation is a complex organism. It has a structure and a function. There is a logic that drives the function and the structure. The structure evolves, and the development is guided by the intended or foreseen functions. Sometimes it works the other way as well; because of developments happening in components, some devices get developed. Then, new, innovative applications are created and put out on the market.
Tools and machines
A tool is a device that enhances the strength of a human. It mostly needs a human to wield it. There are also machine tools, where the machine uses the tool to achieve desired modifications in the workpiece. Examples of simple tools are the hammer, saw, and screwdriver.
A machine in our context is an apparatus (a mechanism) that converts a workpiece from one shape to another, which is either ready for dispatch or ready to be further processed by the next machine.
The drive for more industrial automation
Modern industry needs more flexibility. Production volumes need to be scaled up or down. The product mix needs tuning regularly. Rules and regulations change. All this also calls for automation.
Automation components
We can list the components moving from the smallest element to the largest—sensors/actuators, I/Os, drives and motors, the controller (PLC), and the software to program the PLC. All these elements have to be compatible and should be able to communicate with each other so that they work as desired. But you can see that each element has a different function and design. So, it is important to note that the sum of these components is much more capable than any one individual part.
Programmable logic controller (PLC)
The PLC is the brain of the automation system. As the name suggests, the PLC is an electronic component that can be programmed as per the needs of the user. The program can be written, deleted, or re-written in the PLC. The data from the machine operations is also written and stored in the PLC. The PLC is identical to your computer or laptop. It has a processing chip, a motherboard, random access memory (RAM), read-only memory (ROM), a clock, storage space, Ethernet ports, and USB ports. In the industry, it can either be a microprocessor-based, field-programmable gate array (FPGA) or an industrial PC:
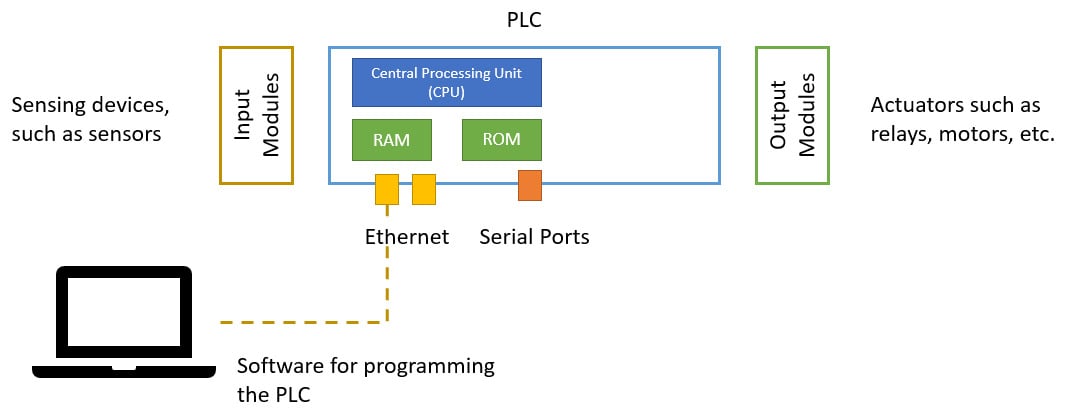
Figure 1.8 – An architecture of the PLC with hardware and software functions
Software is needed to program these PLCs, which we will see in the upcoming subsection, Programming software and tools. This software is installed on a laptop or a desktop, and the developer then connects their laptop with the PLC for programming it.
Inputs and outputs (I/Os)
Just like our hands, ears, nose, tongue, and eyes are the sensory organs and provide the necessary information to our brain, some inputs are required for the PLC to function efficiently and take necessary actions. When we pick up something that is very hot, our fingers realize it and send signals to our brain, to which our brain responds by most probably dropping the object we picked up and holding our hand in cold water. Thus, the input from our finger is translated into action.
Similarly, the PLC needs inputs from various devices, such as sensors, to gather information about what is happening in the machine to take necessary action. I/Os in automation are extremely essential elements. As we saw earlier, inputs are needed to gather data from the field from sensing devices, and outputs are needed to take action based on the inputs received from the field. The software inside the PLC converts the raw data from the inputs into actionable information. Let us take an example of a tank being filled with water having two sensors for sensing the levels—one at the bottom and another at the top. When the sensor at the bottom is not triggered (sensed), then normally, the tank is empty, and water should be filled into the tank. When the sensor on the top is triggered, that means the tank is full, and the water filling should stop and remain stopped until the sensor at the bottom is once again not triggered. However, as a programmer, you need to take care of faulty sensors. What would happen if the sensor at the bottom is faulty and shows an indication that it has not been triggered , but the tank is full? The programmer needs to understand these possibilities and program accordingly. In addition, apart from these sensors, the market also provides analog ultrasonic sensors for measuring levels. We will study these in detail in Chapter 4, Level Control: Controlling the Level of Liquid to Avoid Drying Up or Spilling Over.
Typically, signals are ideally either digital or analog. A state of 0 or 1 represents off and on, respectively. A digital input, as well as digital output, has the same binary representation of 0 and 1. When you need to start a machine and you press a button, the input ‘on’ (binary 1) is sent to the PLC. This is a momentary push of a button. The moment the button is released, the signal changes to ‘off’ (binary 0). Similarly, to start an operation, a PLC needs to send an ‘on’ (binary 1) signal to the device and if you need to stop the device, then an ‘off’ (binary 0) needs to be sent to the device.
On the other hand, analog signals have a range that might be 0 to 65,535 or –32,768 to 32,767 and can be scaled to identify the actual value. Typically, analog signals are used for frequency, pressure, temperature, and flow.
Sensors and actuators
As described in the Inputs and outputs (I/Os) subsection, the sensors are connected to the inputs and the actuators are connected to the outputs of the PLC. Sensors are, let us say, the eyes and ears of the controller, whereas actuators are the arms and legs. Similar to our sensory organs, the sensors sense changes in the machine and provide them as inputs to the PLC. The PLC, in turn, runs the program and decides what the predefined actions are that are needed after particular inputs are activated. Let us again take the example of the water tank. What is the meaning of filling water? In most common situations, water would be filled into the tank by either turning on a valve or switching on a motor. These are outcomes of switching on outputs from the PLC and physically connecting them to the motor or the value activating them. When the motor or valve is switched on, there could be feedback to check whether they are actually turned on. These are all various possibilities, and the programmer needs to take care of these aspects.
There are many types of sensors, such as capacitive and inductive, that provide digital signals to the PLC and need digital inputs for detecting these inputs. There are also sensors that are analog in nature; that is, they provide inputs in the value range of 0 to 65,535 and need an analog input to sense these signals. There are also sensors that provide pulse-width-modulated signals, and some are high-speed inputs that need special input modules. There is a large set of potential inputs, and we have only covered some basics in this section.
Similarly, there are different types of outputs for various actuators, such as a digital output providing signals in 0 or 1 for actuating the output. There are relay-type outputs too. Outputs also come in the form of analog outputs where the activation of the outputs varies from 0 to 65,535. There are pulse-width-modulated outputs as well as high-speed outputs.
The following is a list of some of the sensors used in automation:
- Inertia measurement units: This is a unit that includes a set of accelerometers and gyroscopes
- Temperature and humidity sensors: These compensate for errors due to thermal expansion
- Angle sensors (encoders): These calculate the exact positions of arms and end effectors
- Load cells: These avoid system malfunctions and breakdowns
- Vision systems: These are used for identifying objects, especially for pick-and-place operations
The following are examples of basic actuators:
- Stepper motors: These are used for high accuracy
- Servo motors: These are used for better control of the overall system
- Pneumatic and hydraulic actuators: These are usually used for higher load capacity
Drives and motors
There are very few machines that do not have moving parts and that do not need drives or motors. Thus, most machines have some form of motion components. There are servos, steppers, variable frequency drives, and motors connected to them for controlling moving parts.
Depending on the precision needed, the machine builder will choose between a stepper, variable frequency, or servo drive. Indeed, the cost implications also change based on the choice of drive and motor.
Robots, too, are controlled by drives and motors. A six-axis robot has six motors and associated drives; a Selective Compliance Articulated Robot Arm (SCARA) robot (a type of industrial robot) or a delta robot has three motors and associated drives.
All motion components are controlled by the PLC in various forms. There are different ways to control these motion components, and we will take a detailed look at them in Chapter 5, Motion Control – Control, Synchronization, and the Interpolation of Axes for Accuracy and Precision.
Programming software and tools
Beyond the hardware components such as I/Os, PLCs, drives, and motors that we have examined till now, there is an important component—software. Software permeates all components of automation. As much as it is a physical presence, the software also determines the function of the parts.
PLC is the brain of the system, but what powers it is the software. A PLC without software is like a car without an engine. PLC is merely a hardware component, and the same piece of hardware is used in different applications. What differentiates the PLC is the software. If for any reason the PLC fails, the hardware can be replaced, and the machine can be brought back to life by simply exchanging the software. This is exactly like when you change your phone; with a few clicks, all data can be brought back to your phone.
As we can see, the software defines the way a system performs and works. Thus, software is becoming an increasingly essential element in machine and factory automation.
A piece of software can be primarily classified as system software, application software, and libraries.
Let us now look at system software. System software means the operating system and libraries. Like with every CPU, to address the CPU directly from user code is very dangerous. This is because usually in programming there are variables that are either entered by the user or holding intermediary calculations. However, there is also a possibility to reference the storage space where the variable is stored. With this, we directly use variables to work with or address the CPU from a user code. If such codes are wrongly implemented, there are chances that the CPU will shut off and go into an unknown state. CPUs have functions and code that differ from version to version, revision to revision. The operating system provides uniform access to the CPU. For industrial automation purposes, we need to react to events in real time; hence, we need a real-time operating system (RTOS). System libraries are common functions that are used in every application. The manufacturer generally provides these functions along with the operating system.
Application software is the area to which the automation engineer/programmer devotes the most time and attention. This software is user-specific, and it provides the functionality that the machine builder/machine user actually needs. With the same controller, machines can be made to perform very different functions using different application software. All algorithms that are used for different control purposes are implemented in the application software.
Algorithms and products
Automation is mainly always experienced by automation engineers in terms of algorithms and products. The operating system and other libraries are only of concern to the more experienced programmer. The developer’s view of the actual functionality focuses on the logic and algorithms that produce a good product. The definition of a good product (end product), and what features the product must have, is defined by the manufacturer of it, who we will call the end user (from the machine builder’s, automation vendor’s and programmer’s perspective). The end user is usually a manufacturing plant or factory.
From this point of view, automation is viewed by what it actually delivers. It is understood by the functionality. It may be controlling temperature, tension control, or the control of the position of a machining tool tip.
Indeed, the rest of our discussion throughout this book will be about products, which algorithms are used in the manufacture of these products, and how there are surprising commonalities in the algorithms used in manufacturing very different products. At the same time, there are startling differences in algorithms of similar parameters, depending on the way the mechanics are constructed.
You should, by now, have a complete understanding of how control systems are deployed in a machine. Moreover, you should also understand how the smaller elements build up to form the entire system.