Analyzing the elements of a factory – production lines and machines
By now, you might have a fair idea about how everyday products are made and eventually how to associate this with the manufacturing landscape and automation. Let us dive deeper into the concepts of the factory, a line, and a machine. I am sure these terminologies must be totally new for many of our readers. A manufacturing setup is primarily split into two main areas, the information technology (IT) infrastructure and the operational technology (OT) infrastructure. As the name suggests, the IT infrastructure in the factory is responsible for handling all the IT activities and managing all data. The production and related automation take place in the OT area. The factory floor is the place where all the machines are lined up in a particular sequence to manufacture a particular product.
Continuous process versus discrete process
There are two types of processes in manufacturing – process automation and discrete automation. Process automation can also be termed as continuous process automation; as indicated by the name, it is a continuously operated process. These specific automation possibilities can be together or in separate areas. A continuous process is a process where the end product or finished product is manufactured continuously without a break, and the manufacturing demands this continuous activity. Wherever there are process-based operations, any untimely stoppages usually lead to wastage and losses. Moreover, restarting the process takes a lot of time. It is important to understand that the continuous process is well connected, and an error in any area disrupts the entire process. Thus, these are critical operations and need critical infrastructure for handling such processes.
On the other hand, discrete processes are independent operations where there are links but then any untimely stoppages in one area do not necessarily directly affect the other areas. However, stoppages in discrete processes usually lead to bottlenecks in the system. With discrete processes come the concept of a line and machines. Discrete processes are built up of several machines that, in turn, are connected with one another to form a line. Each machine is responsible for a particular activity or process. A product must move through these machines and undergo processing at each station. Thus, raw material is fed into one end of the line, and a finished product is obtained at the other end. Let us take the example of a soap-making plant.
Soap making combines both areas of continuous process and discrete process. Preparing the soap mixture is a continuous manufacturing process. This forms the raw material for manufacturing the actual soap block that you can find in supermarkets. A brick of soap is first split into smaller soap blocks at the first station. Then these blocks get punched with the brand or the name of the soap at the following station. After this, the soaps are wrapped in branded glossy or carton packaging. There could be multiple stations for wrapping the soaps. A conveyor takes the soap block through each station. At the end of the wrapping line, the soaps are put together in a huge carton and then shipped to the warehouse for further distribution.
Mass/batch production versus customized production
The process described earlier is a form of mass production or batch production. Thus, once the batch is started, the batch will only finish after the raw material is used up. Let us again head to the kitchen to check an analogy. If you have one burner and are already preparing tea, if someone asks you to prepare coffee, you will need to first finish preparing tea. Once you are done preparing tea, only then will you be able to prepare coffee. This is an example of a batch process, where you need to finish one batch before you start a new or a different one. Thus, on a single machine or a line, there could be multiple soaps that might be manufactured. However, before you take up manufacturing a soap of a different scent, you need to finish the batch at hand. You might also need to clean the existing equipment to avoid contamination.
This is a concept that was introduced in automotive manufacturing. On the other hand, individualized production is a relatively new concept where each product can be customized. Today, you can gift chocolates with personalized messages and individual names. You need to pay a premium to purchase such products, but there is immense pleasure in having or gifting a bar of personalized chocolate. With adaptions made to existing production lines, organizations enable such unique possibilities. The major focus for organizations is to have a perfect balance between the cost of producing individualized products and not overburdening the consumer. Simply put, the manufacturing cost cannot be too high and the unique product cannot cost too much. Let us follow an example to better understand this: if a bar of chocolate costs $10 with a manufacturing cost of around $2, then the cost of personalized chocolates cannot be $20 with a manufacturing cost of $12. There will always be a limit on how much premium a consumer is willing to pay for a special product. Thus, the focus for organizations is to keep the costs under control while also offering such unique products that bring something new to the market.
Batch production or mass production provides an organization with cost-effective manufacturing. Moreover, this kind of production methodology is developed to cater to rising demands as well as keep costs in check. Once again, the focus of these innovations and changes is the consumer. As the consumer demands such possibilities, organizations are working toward building such products. In particular, to satisfy the pressure on price, goods need to be manufactured in large quantities at high speed. This is a case for automation.
Inside a factory
Every factory in every industry is a bit different; however, the basics always remain the same. In a factory, there is always an area for the corporate teams that might include research and development, human resources, finance, marketing, management, supply chain, and sourcing, among many others. This forms the office space of a factory. Then there is an area where the goods are manufactured, such as the shop floor. This area forms the OT space inside a factory. There are other areas, such as stocking incoming raw materials, stocking finished goods, the warehouse, and the distribution of products. In larger factories, there could be a possibility that these elements are not in a single area but might be spread over acres of land or even across one city or multiple cities.
There are even factories that are set up in different parts of the country or even the world, while still being connected to each other. There are examples of factories in the US, Europe, China, and India that are connected via the internet for various operations. These are the cases for huge organizations that are spread globally.
Let us now focus on one part of the factory that is of utmost importance for this book—the shop floor.
The shop floor or the factory floor is the place where the products are manufactured. The question is how? The shop floor is made up of different machines. Each machine is responsible for performing a certain action. Let us take the example of preparing a burger in any big burger shop. The bun needs to be toasted, which happens on, say, counter no. 1. A person manning this counter will toast the buns and, once done, will pass on these buns to the next counter. The buns then need to have some sauces applied to them, which takes place on counter no. 2. The person manning the counter then applies sauces on the buns based on the order. The buns also might need the addition of lettuce, which can take place either on a subsequent counter or on the same counter. After this process, this product is moved to the subsequent counter, say counter no. 3, where a deep-fried patty is inserted between the buns. Finally, the burger is ready and then this product is moved to another counter, say counter no. 4, where the burger is packed in a paper carton and sent to the delivery counter. Thus, the counters for assembling the burger are stationary and the product, that is, the burger, makes its way from the first counter to the final delivery to the consumer. There is also a possibility that along with the product, the person manning the stations moves with it or there are different people manning different counters. On the shop floor, these individual counters are called stations and are made up of individual machines. Each machine has a unique role to play. These stations together are termed as a line in the factory. This forms the basis of a machine and a line. A typical line in the packaging industry is shown in Figure 1.5:
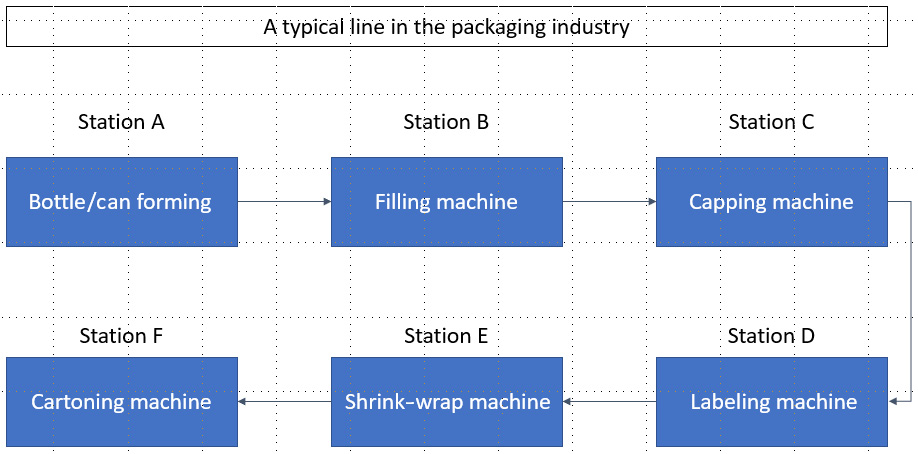
Figure 1.5 – A typical production line in the packaging industry
Figure 1.6 shows a typical production line with various stations, robots, operators, conveyors, and products:
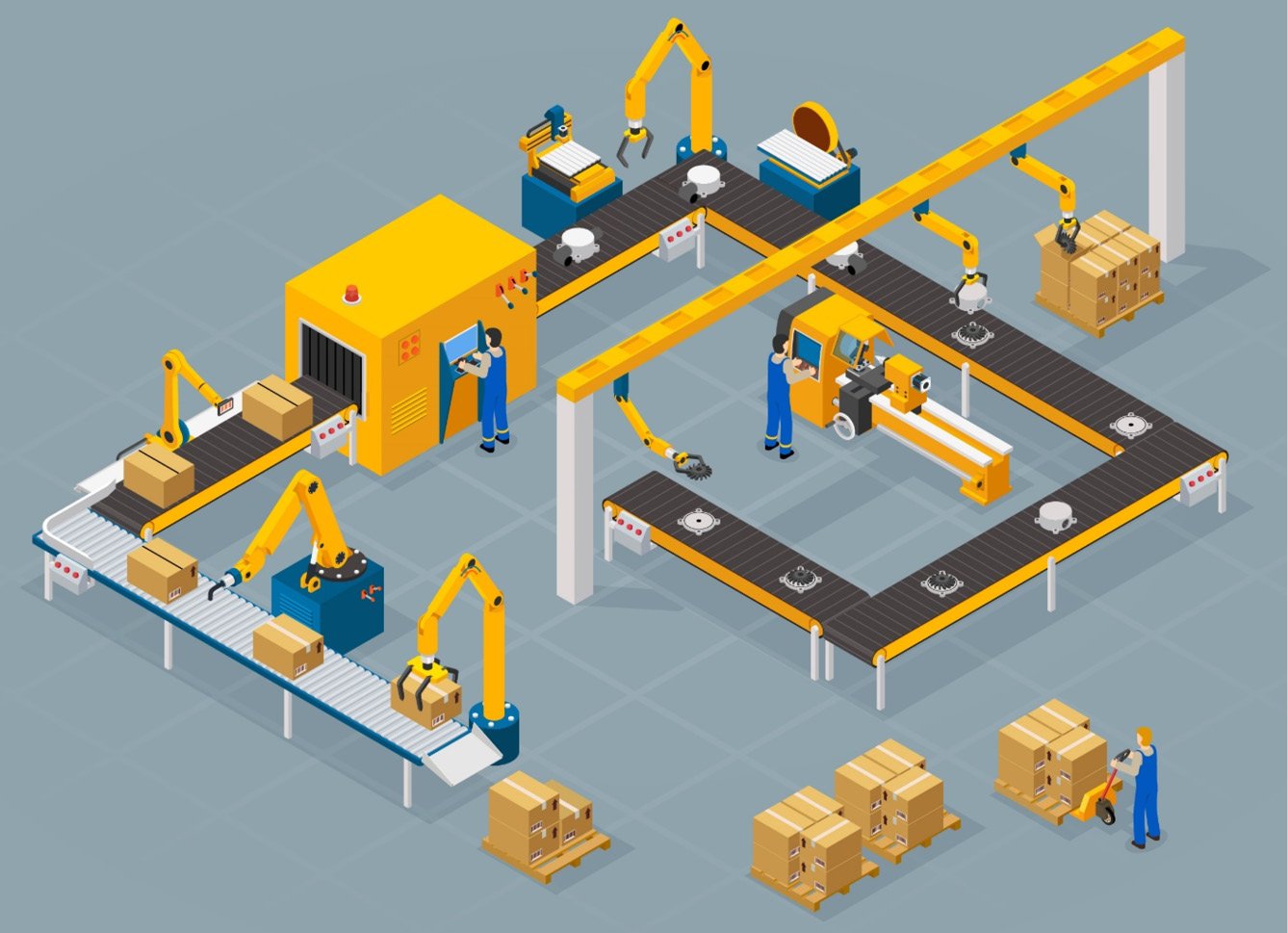
Figure 1.6 – A view of a production line with various stations, operators, and conveyors
An established method, inherited from the second Industrial Revolution, is to divide work on a product. This work or process is repeated on each product at one place called a workstation.
Let us take the example of a factory in the packaging industry to clarify how these concepts add up. In the packaging industry, let us focus on a bottling line where the factory manufactures and fills water bottles.
Water is one of the raw materials, and the factory needs to have a huge storage of water for filling the bottles. The PET bottles are made from a miniature plastic preform that is no more than 10 cm in length. This is another raw material for the bottling factory. This preform is molded into a PET bottle with a capacity of 1 liter using a process called PET blow/blow molding. This is the first station in the factory, where the preforms are blown into the desired shape of a bottle. The bottles are then transferred either manually or on a conveyor and taken to the subsequent station. At this station, the bottles are cleaned and then filled with water. These filled bottles are then moved on to the next station on the same conveyor for capping. After applying caps, the bottles then have labels applied for various purposes, such as branding, compliance assurance, and other information, and then are checked for quality. If the bottles are unequally filled or there are quality issues with the bottles, capping, or labeling, then this station rejects the faulty bottles and only accepts good bottles. After this, the conveyor takes the bottles to either a carton or shrink-wrap station, where the bottles are packaged for transport. A robot then creates a stack of these packaged cartons or shrink-wrapped bottles and they are made ready for storage or dispatch. The conveyor is responsible for transferring the products from one station to another. The stations are individual machines and are controlled by individual controllers, which we will see in the next section.
The line on the factory shop floor is a network of many machines, one after the other, performing different actions in order to manufacture a complete product. A machine is an independent entity that is responsible for performing only one or a set of tasks. Thus, any faults in one machine do not affect the operation of one on another station. However, as discussed earlier, if one station is down, then it leads to a bottleneck, as the previous stations in the line are healthy and producing at full speed, and the stations after the faulty station are healthy but are starved of products, as the station feeding them with products is broken down. Thus, as soon as the machine with a fault is back up and running, the line immediately starts operating at full speed. Systems resuming with a healthy status and returning the entire line in a factory to full speed operation is a scenario that is usually possible in discrete manufacturing with machines and lines; however, this is unlikely in a continuous process.
It is possible that inside a factory there could be multiple lines and tens to hundreds of machines on each line. There is the possibility that an entire building is dedicated to one line and there might be multiple buildings/shopfloors that constitute a factory. It is also possible that in one building there could be multiple lines for different products. In a printing press, there could be four lines printing different newspapers of the publication in different languages. In the case of a packaging line, there could be three parallel lines that are manufacturing, packaging, and cartoning different types of cookies/biscuits of the same brand. In the case of an automotive factory, there might be different buildings for the body shop, the paint shop, the engine line, the chassis line, and the final assembly, with each line having different machines and robots.
As we are now familiar with the elements of the factory, lines, and machines, let us go a step further and understand the finer elements of a machine.