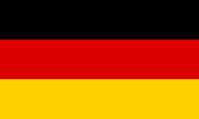
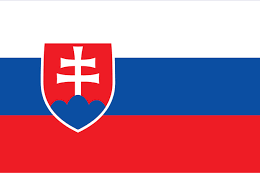
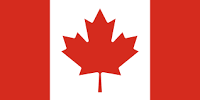
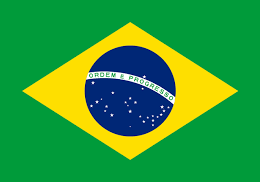

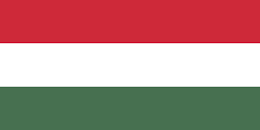
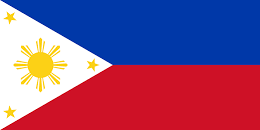
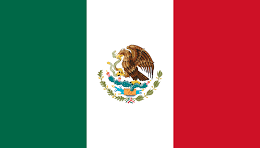
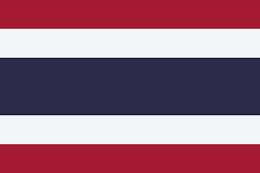
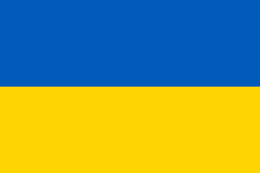
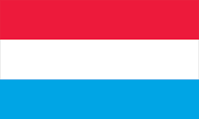
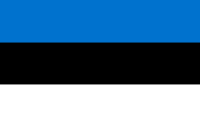
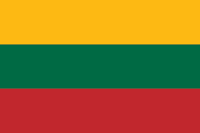
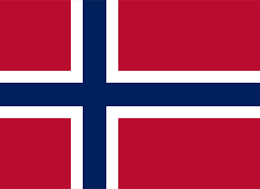
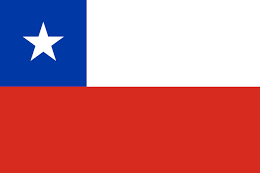
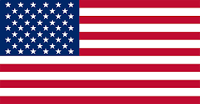
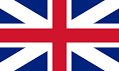
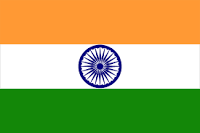
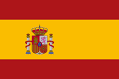
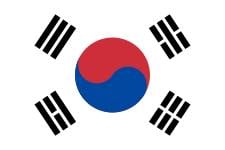
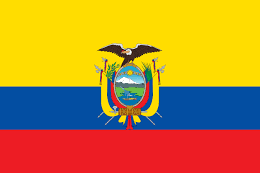
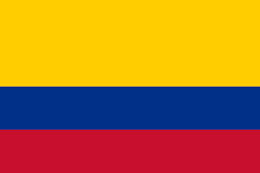
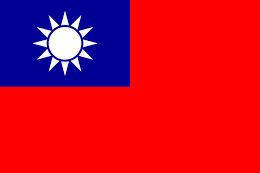
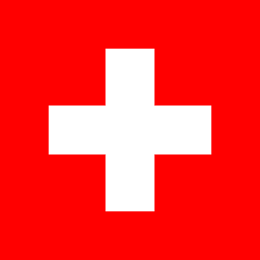
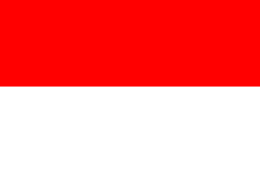
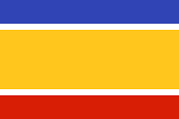
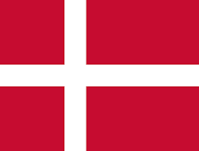

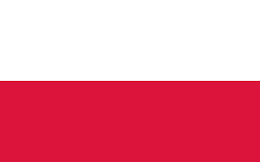
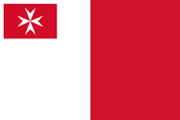
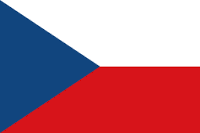
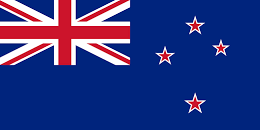
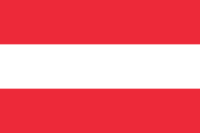
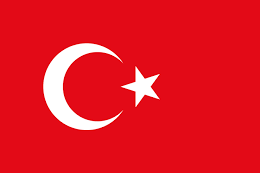
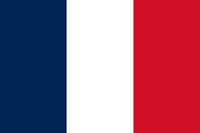
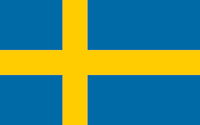
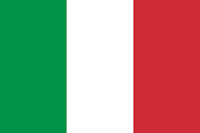
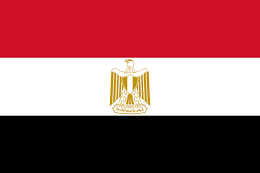
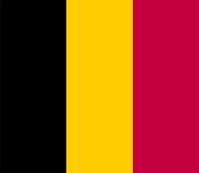
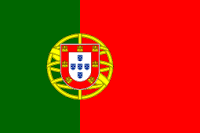
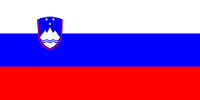
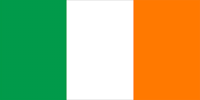
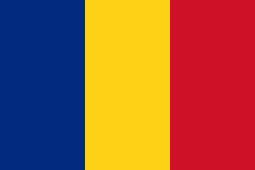
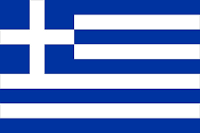
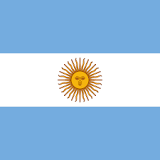
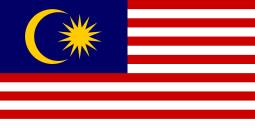
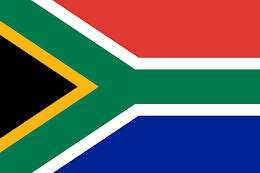
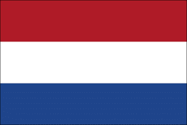
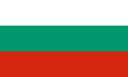
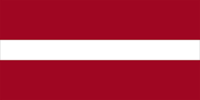
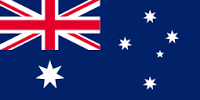
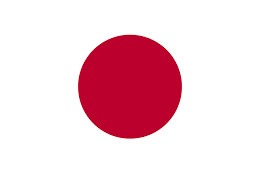
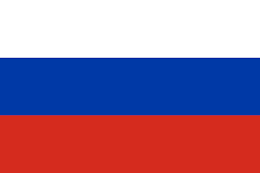
Although solderless breadboards provide makers with an easy way to build functioning circuits and software, the builds are only really reliable if they aren't handled too heavily. For example, in our first post, we talked about building a Weather Cube as a sensory tool for occupational therapists. The breadboard circuit and the foam cube secured inside this might survive fairly well, but for any highly-physical wearable applications, it would be easy for a single wire to be pulled out of the circuit, causing it to fail at a vital moment.
In this post, we will detail how we soldered our Weather Cube project, plus provide you with timesaving and pain-saving tips born through trial and error (and one burnt finger). If you have very little or no experience working with stripboards, it could be worth practicing your skills before starting.
Protective equipment such as safety glasses should always be worn. You should also have first aid equipment available whenever working with metal, including melting solder, hacksawing, and spot-cutting copper board.
Before you begin soldering your project, you will need the following:
First, cut your stripboard (also called veroboard by some people, but it's the same thing). Do this by laying the stripboard horizontal, with the copper side facing you. Count 25 points from the middle, right, and side of the stripboard. Draw a line from top to bottom. Use a G-clamp to secure your stripboard to a solid surface, and then cut along the line with your junior hacksaw.
Starting with just downward strokes will help you keep on track initially. You could also cut the top two rails off if you want your project to be as small as possible, or color the top two rails to remind yourself not to count these holes.
Then, follow these steps:
A piezo is a small sensor device used by Makers to convert pressure and force into an electrical charge. These sensors are also very delicate, and can easily come apart. If it does, you will have to re-solder it.
To solder the piezo back together, follow these steps:
Soldering can provide projects with greater robustness, allowing them to be handled without easily falling apart. With these steps, we hope to have provided you with some of the tips and tricks to successfully solder your inventions.
Clare Bowman enjoys hacking playful interactive installations and co-designing digitally fabricated consumer products. She has exhibited projects at Maker Faire UK, Victoria and Albert Museum, FutureEverything, and Curiosity Collective gallery shows. Some recent work includes “Sands Everything”, an interactive hourglass installation interpreting Shakespeare’s Seven Ages of Man soliloquy through gravity-controlled animated grains, and more.
Cefn Hoile sculpts open source hardware and software, and supports others doing the same. Drawing on 10 years of experience in R&D for a multinational technology company, he works as a public domain inventor, and an innovation catalyst and architect of bespoke digital installations and prototypes. He is a founder-member of the CuriosityCollective.org digital arts group, and a regular contributor to open source projects and not-for-profits. Cefn is currently completing a PhD in Digital Innovation at Highwire, University of Lancaster, UK.