Identifying waste and constraints
Success in the business – whether commercial, government, or non-profit – is not just determined by how well you can add value but also by how proficiently you can prevent value leakage. Inefficiencies, if left unchecked, can erode an organization’s competitive edge, resulting in wasted resources, missed opportunities, and diminished profitability. In this section, we will delve into the art and science of pinpointing wasteful constraints and effectively weeding them out, empowering you to champion operational excellence in your professional journey.
Viewing the spectrum of waste
Waste can manifest in obvious forms, such as a defect in a manufactured product, or more subtle ways, such as an unnecessary approval step in a process flow. To holistically address inefficiencies, you must first be adept at identifying waste in all its forms. The general categories for Lean-oriented waste are listed in Figure 3.4, for both traditional and software categories:
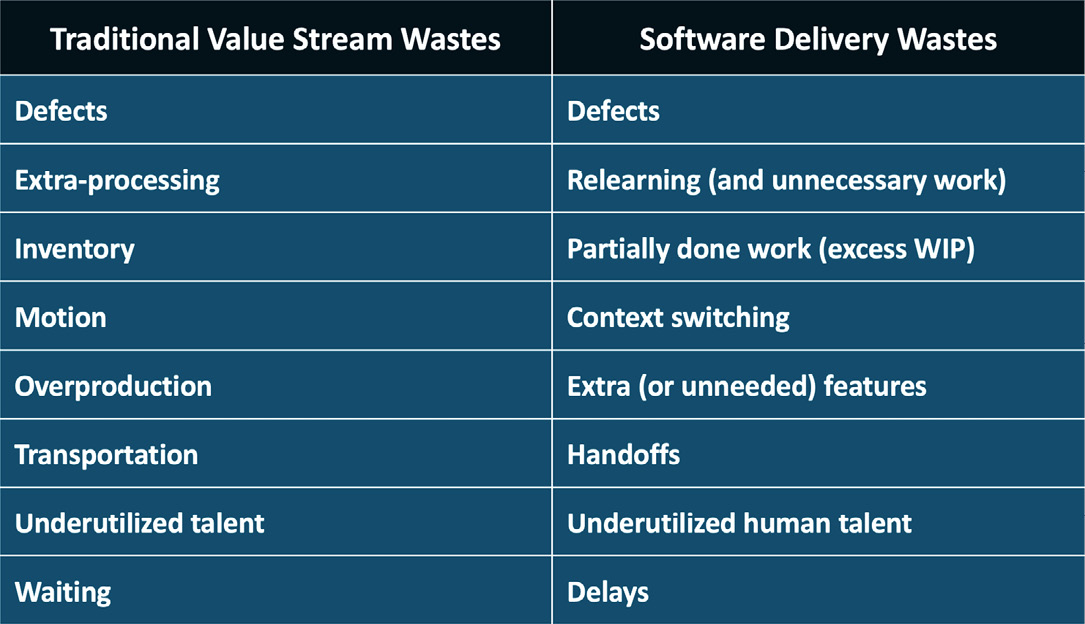
Figure 3.4 – Types of waste
As noted previously and shown in the Traditional Value Stream Wastes column of Figure 3.4, Lean practices have historically delineated eight primary forms of waste. Let’s look at these in more detail:
- Defects: Defects and poor quality lead to rework and corrections, consuming valuable resources and potentially damaging customer trust.
- Overproduction: Producing more than is required can tie up resources and capital, resulting in unnecessary storage, increased costs, and potential obsolescence.
- Waiting: Delay time between processes indicates inefficiencies and can increase the overall production timeline. Waiting can be an indicator of upstream bottlenecks, insufficient supplies, dependencies, too much work in process (WIP), lack of automated processes and more.
- Non-utilized talent: Failing to use the skills and knowledge of employees leads to overlooked innovations and ideas, underutilized skills and expertise, and diminished learning opportunities and productivity.
- Transportation: Unnecessary movement of products or materials adds costs and can increase the risk of damage or loss.
- Inventory excess: Holding excessive inventory ties up capital, consumes space, and can lead to spoilage or obsolescence, all of which add to our costs.
- Motion Waste: Redundant or unnecessary motions by workers can lead to inefficiencies and increase the risk of injury.
- Extra-processing: Adding more steps than required to a process or over-engineering a product can consume resources without adding value to the end customer.
While these classifications sprouted from manufacturing, their essence is universally relevant. Whether you’re in software development, financial services, or healthcare, these waste categories can provide a structured lens to evaluate processes and identify inefficiencies. Still, it is often valuable to tweak the list of wastes to reflect the variances across domains of work, as we have done in the following subsection for software-oriented waste.
Tweaking elements of waste by domain
We’ve touched upon the traditional eight types of waste that are applicable across various industries. However, fine-tuning them to specific contexts can enhance their relevance. For instance, in a digital service firm, “inventory excess” might pertain to unused software licenses , incurring needless expenses. Similarly, “motion waste’ could be reflected in frequent handoffs during a project, leading to delays and possible communication breakdowns.
So, let’s see how the concept of Lean-oriented waste translates into software development:
- Defects: In the software realm, defects lead to buggy applications, diminished user experience, and increased maintenance efforts.
- Relearning (also unnecessary work): Redoing tasks or revisiting solved problems due to poor knowledge retention or documentation wastes time and delays progress.
- Partially done work (excess WIP): Having excessive WIP can obscure the project’s actual state, reduce agility, and delay the realization of value.
- Context switching: Constantly shifting focus between tasks or projects reduces efficiency, forces relearning, and can lead to increased errors or missed details.
- Extra/unneeded features: Developing unnecessary features consumes resources, complicates the user experience, and can make the product overly complex and challenging to use, all of which are non-value-added from our customers’ perspectives.
- Handoffs: Passing work between teams or individuals can lead to communication breakdowns, potential bottlenecks and delays, and a dilution of responsibility.
- Underutilized human talent: Not harnessing the full potential of software professionals can lead to missed innovative solutions and decreased morale.
- Delays: Waiting for decisions, feedback, or dependencies can hinder progress, delay releases, and frustrate teams.
By classifying and understanding these waste forms, you will equip yourself to effectively spot and address inefficiencies across various product lines and service offerings. But now, we need to move on and discuss perhaps the most critical issue, which is constraints.
Constraints – the silent value blockers
While waste can be seen as actions or steps that add no value, constraints are barriers that actively hinder value delivery. A constraint could result from excessive cycle times or setup times creating a bottleneck in a manufacturing line, a software server that can’t handle required transaction volumes, or even an organizational policy that impedes rapid decision-making.
Recognizing these constraints is paramount. The Theory of Constraints (ToC), a management paradigm developed by Eliyahu Moshe Goldratt – outlined in his book The Goal, posits that in any complex system, there’s often one major limiting factor that defines the system’s capacity.3 Let’s look at Figure 3.5 to see the value of identifying our constraints:
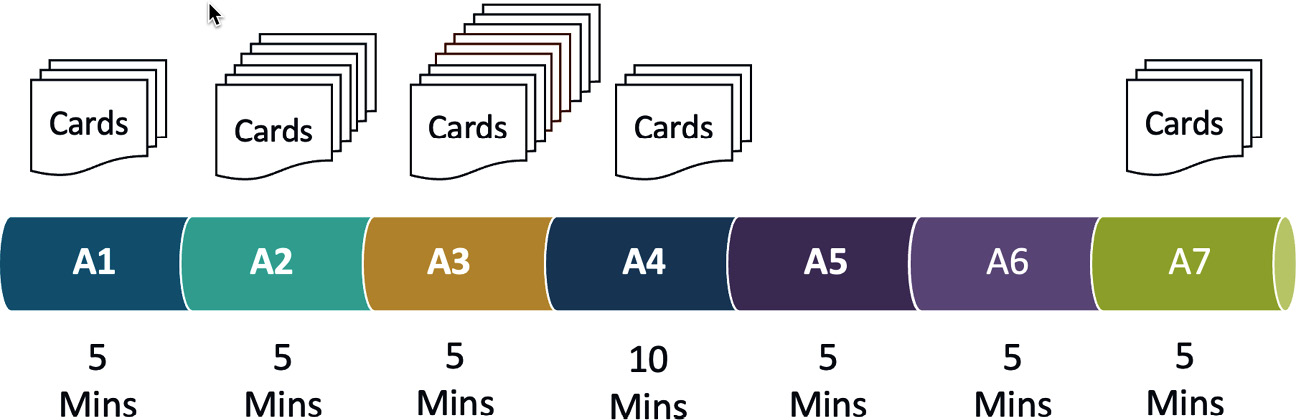
Figure 3.5 – ToC example
Figure 3.5 depicts a value stream comprising seven activities, each taking 5 minutes, with one exception: a central activity (A4) that requires 10 minutes. This lengthier activity creates a bottleneck, causing a backlog of work in the steps leading up to it. Meanwhile, subsequent activities lack work, awaiting input from the bottlenecked step.
At this point, we may not know why it takes 10 minutes to complete activity 4. For example, it could be the result of a lengthy setup, the work duration, an inspection process, or waiting on information, materials, or resources causing the delays. However, by identifying and addressing this constraint, we can significantly elevate the system’s performance.
Eliminating constraints is pivotal for optimizing workflow and maximizing value. By prioritizing waste removal based on constraints, organizations can address the most impactful bottlenecks first, ensuring smoother processes and heightened efficiency.
In your professional journey, understanding the concept of constraints is invaluable. Not only does it allow you to enhance operational flow in your respective domain, but it also positions you as a strategic thinker capable of holistic problem-solving.
Mapping a value stream
In the previous subsection, Figure 3.5 provided a very simple graphical representation of a value steam flow. Usually, our real-life value streams are much more complex, plus we need to capture more information on materials and information flows.
Figure 3.6, or the enlarged version in Appendix A: Machine Shop Value Stream Example, shows a value stream map for a manufacturing line. Since it’s not the focus of this book to teach value stream mapping practices, we will not spend time here going through this map. Instead, we’ll spend our time going through the mapping process.
However, for those who want to take a detailed dive into the mechanics of value stream mapping, Author Cecil Rupp goes into this topic extensively in his previous book, Driving DevOps with Value Stream Management. 4 The Further reading section also includes references to several well-known books on this topic. 5,6,7,8,9,10
In Figure 3.6, text readability is not critical; the diagram is meant to provide an graphical depiction of flows across of a automotive manufacturing line:
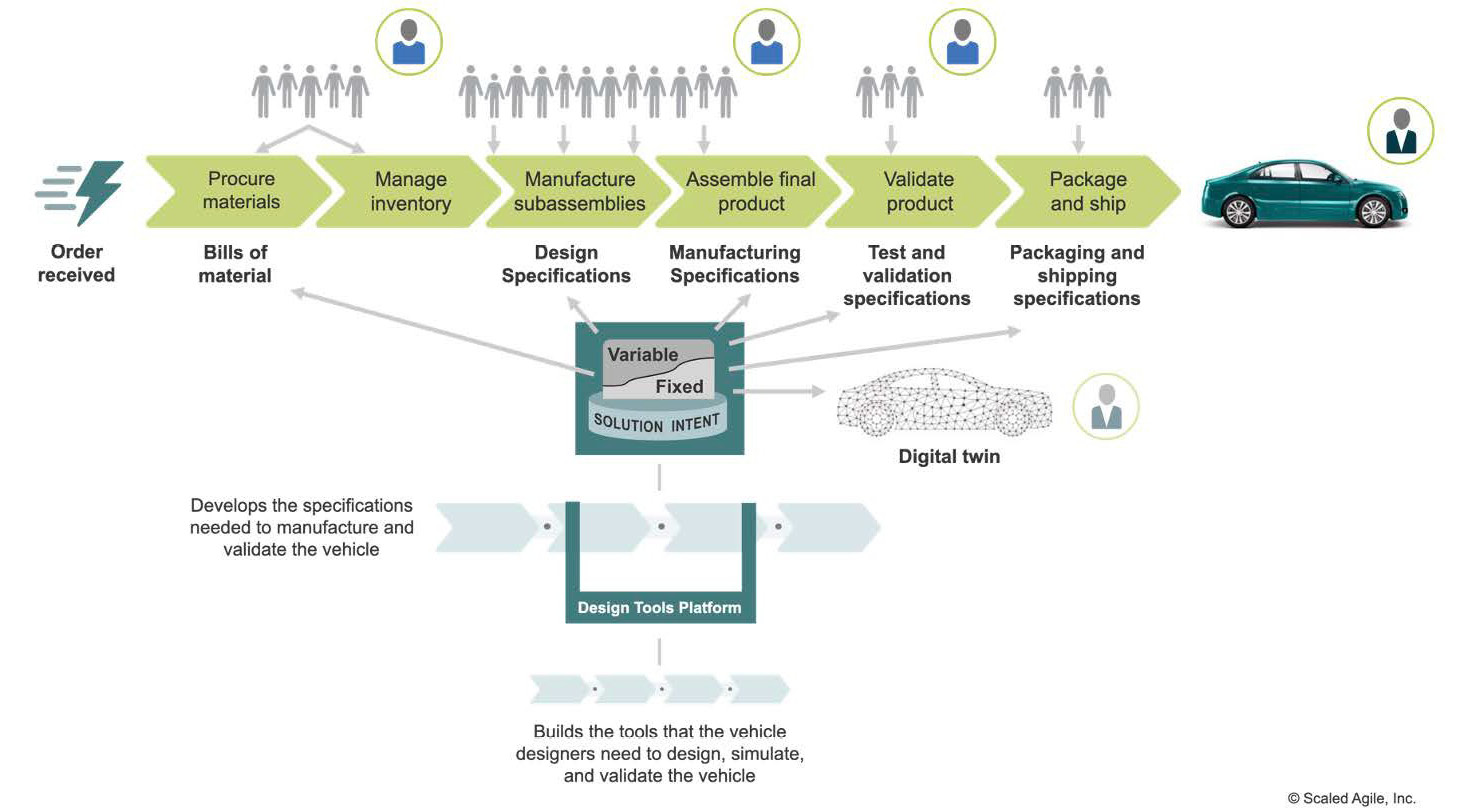
Figure 3.6 – Manufacturing value stream map example
Value stream mapping is a visual tool originating from Lean manufacturing that is used to analyze and design the flow of materials and information required to bring a product or service to a consumer. The goal is to identify waste and areas of improvement within processes.
Figure 3.7 provides a quick overview of the work involved in mapping a value stream:

Figure 3.7 – Value stream mapping and improvement process
Here is a concise summary of the mapping process, consistent with Lean practices:
- Identify the product/service: Begin by choosing a product or service to map. This should be something that is critical to your business, or a process that is known to have issues or inefficiencies.
- Define the scope and boundaries: Clearly define the start and end points of the process you are mapping. This might be from the moment an order is placed until its delivery or from raw material to finished product.
- Gather a cross-functional team: Assemble a team with representatives from each function involved in the value stream. This will provide multiple perspectives and a holistic understanding of the process.
- Map the current state: Start by mapping the current state of the process as it operates, not as you think it operates. Document the steps, flows, and information necessary to deliver the product or service. This typically includes the actions, inventory, waiting times, and information flows that occur as a product or service moves through the process.
- Collect data: For each step, gather data such as cycle time, wait time, defect rates, inventory levels, and any other metrics that indicate how the process is performing. This quantitative data is crucial for identifying bottlenecks and waste.
- Identify waste: Within the map, distinguish between steps that add value from the customer’s perspective and those that do not (waste). Non-value-added steps are targets for improvement.
- Map the future state: Using the current state map and the collected data, design a future state map that shows how the process should operate after the waste has been removed or reduced. Focus on creating a flow that delivers value as efficiently as possible, minimizing wait times and reducing non-value-added steps.
- Create an action plan: Develop a plan to transition from the current state to the future state. This includes assigning tasks, setting deadlines, and determining the resources needed to implement changes.
- Implement changes: Execute the action plan, make the necessary changes to the process, and ensure that all team members are trained in the new process.
- Review and continuously improve: After implementing changes, monitor the process to ensure that improvements are sustained. Regularly revisit the value stream map to identify further areas for improvement. Repeat the process for the next value stream.
In Chapter 4, Driving Improvements with Value Stream Management (VSM), we’ll dive a bit more deeply into the approach to identify and prioritize the most impactful improvement opportunities.
By visually laying out all the steps in a process and linking them to the flow of information and materials, value stream mapping allows you to see the sources of waste and any inefficiencies. With this insight, teams can collaborate on a targeted approach to creating more value for the customer with less work, which is the essence of Lean.
Amplifying IT’s impact – driving operational efficiency and strategic value
Why is all of this vital to your professional career in IT? In today’s landscape, where margins are slim and competitors are relentless, achieving operational efficiency is essential. By adeptly identifying and reducing inefficiencies, you enhance the organization’s capacity to deliver value both swiftly and economically. Being in IT, you’re positioned uniquely to champion and implement digital improvements across products, services, processes, and value streams.
The benefits extend directly to the bottom line. Minimizing waste translates to conserving resources by not spending them on activities that don’t add value. By addressing bottlenecks, you ensure timely and effective product or service delivery, meeting market demands head-on. Such expertise doesn’t just boost profitability; it heightens customer satisfaction and elevates the brand’s stature.
Moreover, organizations today are on the lookout for professionals who don’t just execute tasks but think critically about enhancing value delivery. By mastering the skills of waste identification and constraint recognition, you position yourself as an invaluable asset, capable of driving strategic improvements and fostering a culture of continuous enhancement.
Prioritizing efficiency – the Lean imperative for organizational success
Inefficiencies, whether from waste or constraints, are a common challenge for organizations. Yet, they can be addressed and mitigated. With the Lean principles and practices detailed in this section, organizations can systematically address these inefficiencies, ensuring a smoother flow of value. As the business landscape grows more competitive, the ability to harness efficiency becomes crucial. It allows organizations not only to deliver value effectively but also to maintain profitability. By adopting Lean, organizations are investing in their sustained success and reinforcing their commitment to operational excellence.
This completes our section on identifying waste and constraints. In the next section, we’ll focus on the approach to streamlining value stream flows.