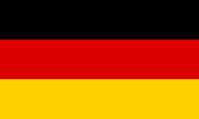
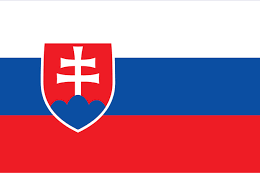
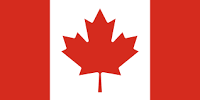
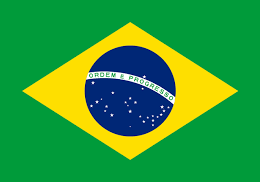

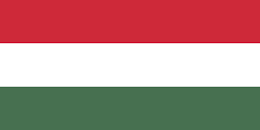
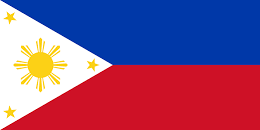
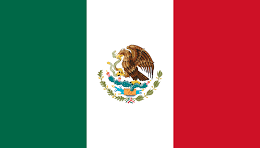
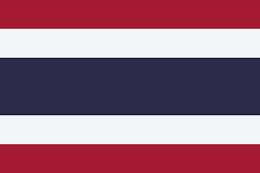
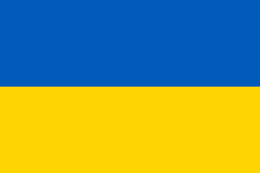
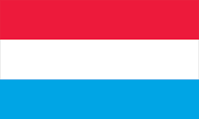
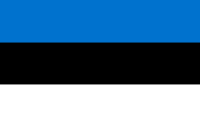
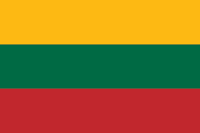
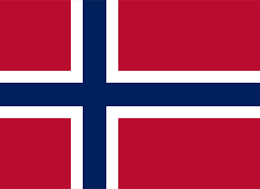
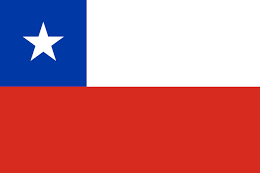
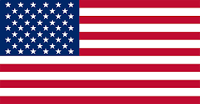
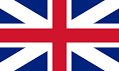
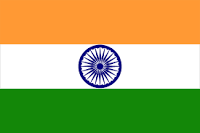
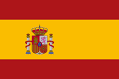
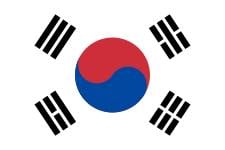
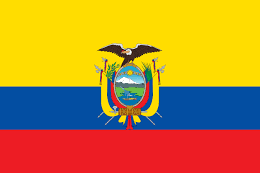
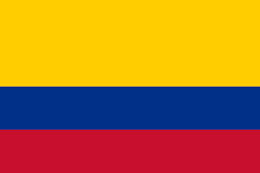
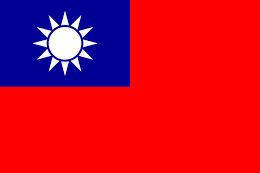
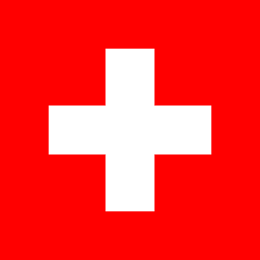
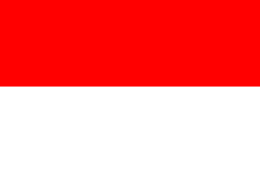
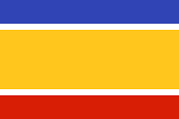
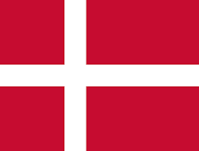

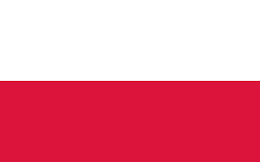
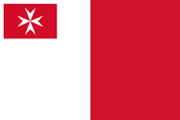
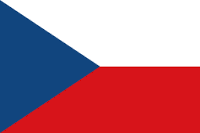
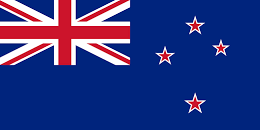
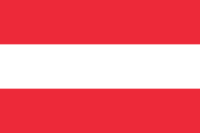
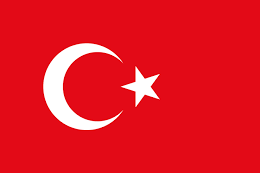
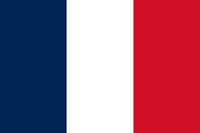
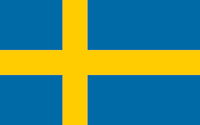
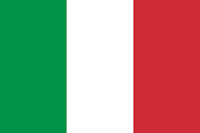
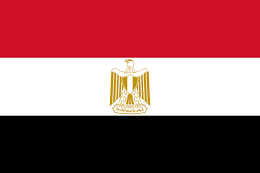
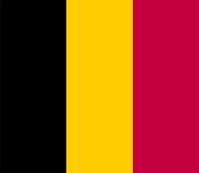
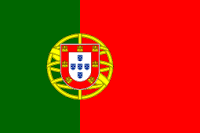
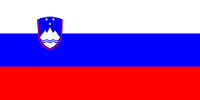
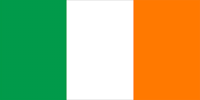
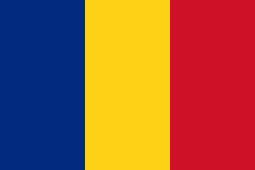
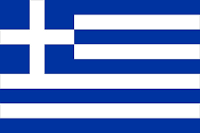
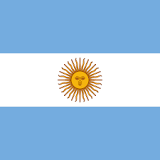
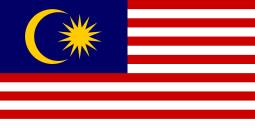
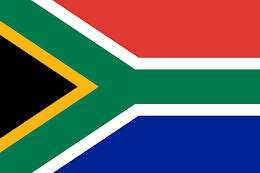
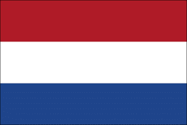
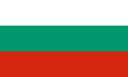
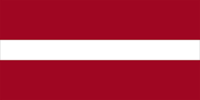
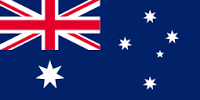
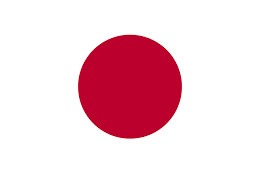
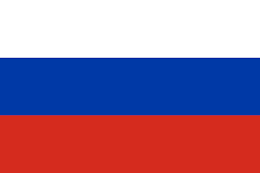
Have you ever wondered where the filament for your 3D printer comes from and how it’s made? I recently had the chance to visit 3dk.berlin, a local filament manufacturer in Berlin. 3dk.berlin distinguishes itself by offering a huge variety of colors for their filament. As a designer it’s great to have a large palette of colors to choose from, and I chose 3dk filament for my Polygon Construction Kit workshop at Thingscon 2015 (they’re sponsoring the workshop). Today we’ll be looking at how one filament producer takes raw plastic and forms it into the colored filament you can use in your 3D printer.
Some of the many colors offered by 3dk.berlin
3dk.berlin is located at the very edge of Berlin, in the area of Heiligensee which is basically its own small town. 3dk is a family-owned business run by Volker Bernhardt as part of BERNHARDT Kunststoffverarbeitungs GmbH (that’s German for "plastics processing company"). 3dk is focused on bringing BERNHARDT’s experience with injection moulded and extruded plastics to the new field of 3D printing.
Inside the factory neutral-colored plastic pellets are mixed with colored "master batch" pellets and then extruded into filament. The extruding machine melts and mixes the pellets, then squeezes them through a nozzle, which determines the diameter of the extruded filament. The hot filament is run through a cool water bath and coiled on large spools. Conceptually it’s quite simple, but getting extremely consistent filament diameter, color and printing properties is demanding. Small details like air and moisture trapped inside the filament can lead to inconsistent prints. Bigger problems like material contamination can lead to a jammed nozzle in your printer.
3dk spent 1.5 years developing and fine tuning their machine before they were satisfied with the results to a German level of precision. They didn’t let me to take pictures of their extrusion machines since some of their techniques are proprietary but you can get a good view of a similar machine in this filament extrusion machine video.
Florian (no small guy himself) with a mega-spool from the extrusion machine
The filament from the extrusion machine is wound onto 10kg spools - these are big! The filament from these large spools is then rewound onto smaller spools for sale to customers. 3dk tests their filament on a variety of printers in-house to ensure ongoing quality. Where we might do a small print of 20 grams to test a new filament, 3dk might do a "small" test of 2kg!
Test print with a full-size plant (about 4 feet tall)
Why produce filament in Germany when cheaper filament is available from abroad? Florian Deurer from 3dk explained some of the benefits to me. 3dk gets their PLA base material directly from a supplier that does use additives. The same PLA is used by other manufacturers for items like food wrapping. The filament colorants come from a German supplier and are also "harmless for food". For the colorants in particular there might be the temptation for less scrupulous or regulated manufacturers to use toxic substances like heavy metals or other chemicals. Beyond safety and practical considerations like printing quality, using locally produced filament provides local jobs
What really sets 3dk apart from other filament makers in an increasingly competitive field is the range of colors they produce. I asked Florian for some orange filament and he asked "which one?" The colors on offer range from subtle (there’s a whole selection of whites, for example) to more extreme bright colors and metallic effects. Designers will be happy to hear that they can order custom colors using the Pantone color standard (for orders of 5kg / 11lbs and up).
Which white would you like? Standard, milky, or pearl?
Looking to the future of 3D printing, it will be great to see more environmentally friendly materials become available. The most popular material for home 3D printing right now is probably PLA plastic (the same material 3dk uses for most of their filament). PLA is usually derived from corn, which is an annually renewable crop. PLA is technically compostable, but this has to take place in industrial composting conditions at high temperature and humidity. People are making progress on recycling PLA and ABS plastic prints back into filament at home but the machines to make this easy and more common are still being developed.
100% recycled PLA print of Origamix_Rabbit by Mirice printed on an i3 Berlin
3dk offers a filament made from industrially recycled PLA. The color and texture for this material varies a little on the spool but I found it to print very well in my first tests and your object ends up a nice slightly transparent olive green. I recently got a "sneak peek" at a filament 3dk is working on that is compostable under natural conditions. This filament is pre-production, so the specifications haven’t been finalized, but Florian told me that the prints are stable under normal conditions but can break down when exposed to soil bacteria. The pigments also contain "nothing bad" and break down into minerals. The sample print I saw was flexible with a nice surface finish and color. A future where we can manufacture objects at home and throw them onto our compost heap after giving them some good use sounds pretty bright to me!
A friendlier future for 3D printing? This print can naturally biodegrade
Michael Ang is a Berlin-based artist / engineer working at the intersection of technology and human experience. He is the creator of the Polygon Construction Kit, a toolkit for creating large physical polygons using small 3D-printed connectors. His Light Catchers project collects crowdsourced light recordings into a public light sculpture.