Materials available for 3D printing
It used to be that there were essentially only two materials available for 3D printing, Poly-Lactic Acid (PLA) and Acrylonitrile Butadiene Styrene (ABS). This has changed considerably over the last few years. The result has not only given us new materials with which to 3D print; it has changed what we can make with our 3D printers.
Materials used for FDM 3D printing come in the form of a rolled plastic filament of either 1.75 mm or 2.85 mm in diameter. A spool made of plastic, cardboard, or metal is used to hold the filament. Spoolless filament for installing on a reusable spool is also available.
Let's look at the materials we can use for 3D printing, starting with PLA and ABS.
Poly-Lactic Acid (PLA)
PLA is the most used material for 3D printing. It is made from sugar cane or corn starch and is biodegradable, making it an eco-friendly option. Compared to many other filament materials, PLA is extremely easy to work with.
Although not requiring a heated bed (many early 3D printers did not have heated beds), PLA does benefit greatly from heat applied to the bed due to its low melting temperature, which increases its stickiness.
Figure 1.16 shows a part for a small desktop monitor table printed in red PLA:
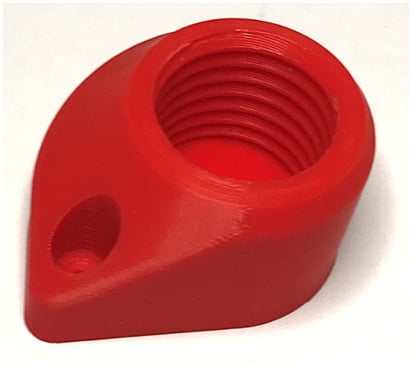
Figure 1.16 – A part printed on the Ender 3 V2
Early PLA was quite brittle, making it unsuitable for many applications, but in recent years PLA has got a lot better, especially in terms of its strength.
When printed at around 200 degrees Celsius at the hot end and 60 degrees Celsius on the bed, PLA provides an excellent finish (temperature may vary with manufacturer).
PLA can be glued with epoxy, providing opportunities to break up larger objects into smaller parts.
Acrylonitrile Butadiene Styrene (ABS)
ABS is another common material for 3D printing and is a popular plastic for making toys. LEGO blocks, for example, are made from ABS.
In Figure 1.17 we see the cat figurine printed in ABS using the G-code file that comes with the Ender 3 V2:
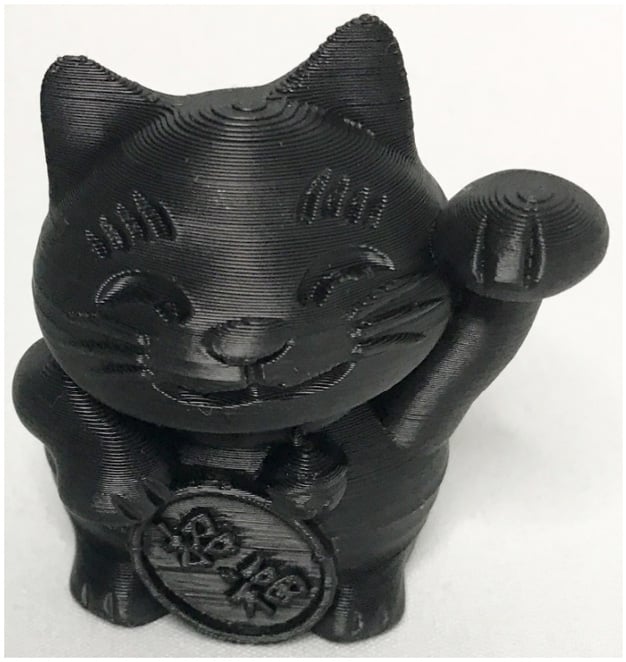
Figure 1.17 – Cat figurine printed with ABS
ABS prints with a certain smell that many find unpleasant and thus printing in a separate room is encouraged.
ABS produces prints that are more durable than PLA and with a higher melting temperature. This makes it more ideal in situations where a part may be subjected to higher temperatures. Having ABS stick to the print bed can be challenging. A heated bed is necessary to produce prints that do not warp upward at the edges and stay flat on the bed throughout the print job. ABS should be printed with a nozzle temperature of around 240 degrees Celsius and a bed temperature of 90 degrees Celsius.
An enclosure is encouraged with ABS printing to avoid cooling cracks on the part during printing.
ABS prints can be smoothed with acetone to hide the layer lines. As we can see in Figure 1.17, layer lines around the top of the print are noticeable. Subjecting our print to an acetone vapor bath will melt the lines together, resulting in a smooth professional-looking 3D print.
An alternative to ABS is ASA, which has similar properties but with UV protection. This makes ASA well suited for outdoor applications.
Glycolyzed Polyester (PETG)
PETG is a modified version of PET (or polyethylene terephthalate), a plastic used extensively in the production of water bottles and food containers since the 1990s. Adding glycol to PET to reduce its brittleness turns it into PETG.
PETG filament prints almost as easily as PLA and provides the strength of ABS with a lower melting temperature. It is known for its impact resistance, light transmission (when transparent filaments are used), and its food-contact safety approval. In Figure 1.18, we see two parts that make up a clamp for a CNC router:
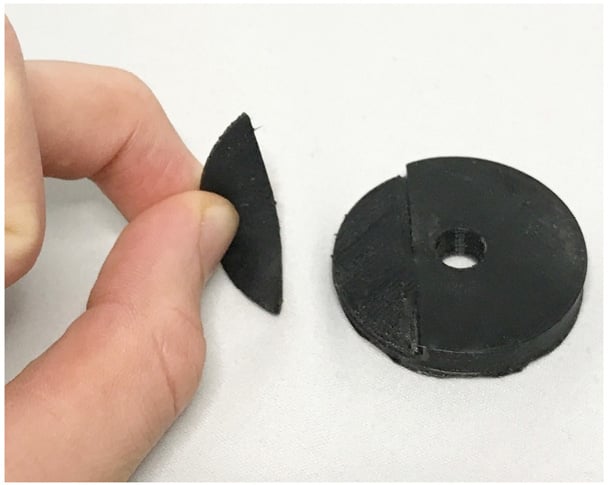
Figure 1.18 – CNC router part made with two different materials
The part on the right was printed with black PETG. PETG parts tend to be shinier and less brittle than PLA. PETG works well for functional parts. It is exceedingly difficult to glue PETG parts together so other construction techniques, such as incorporating nuts and bolts, must be used.
PETG and Glass Beds
PETG should not be printed directly to a glass bed as it sticks a little too well. Removing it from a glass bed can result in chips to the glass and possibly an expensive repair.
High-Impact Polystyrene (HIPS)
HIPS has similar properties to ABS but is lighter in weight. HIPS dissolves easily in d-limonene, making it an ideal dissolvable support material for ABS and other materials. A 3D printer with a dual extrusion system (see Figure 1.19) is required when using a different material such as HIPS as a support material, as shown here:
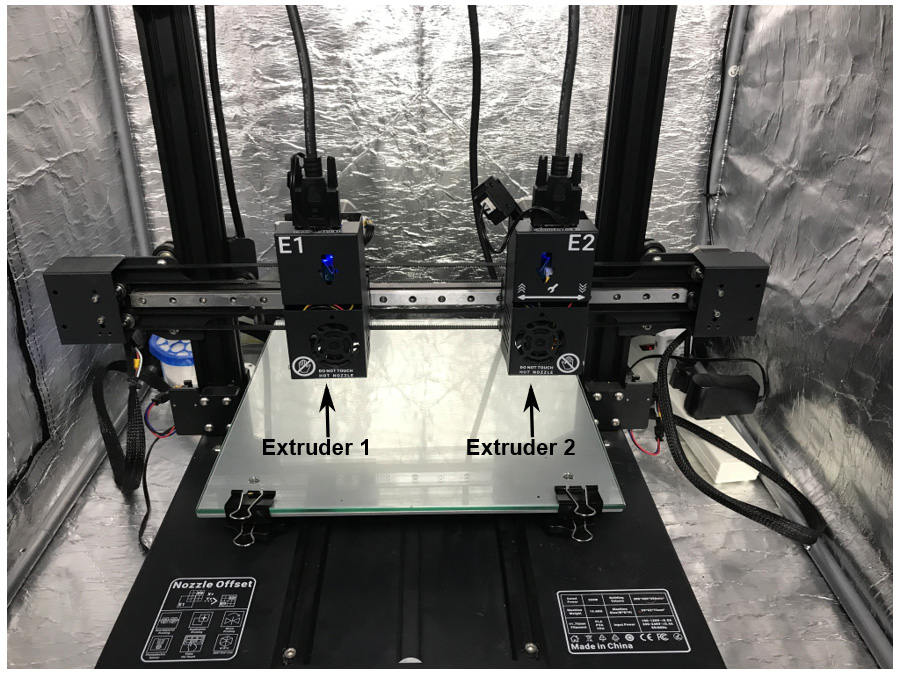
Figure 1.19 – Dual extruder 3D printer
Dual Extruder 3D Printers
Dual extruder 3D printers (not to be confused with dual-gear extruders) use two extruders that move together along the y and z axes but opposite to each other on the x axis. For dissolvable support prints, one extruder extrudes the support material, such as HIPS or PVA, and the other extruder delivers the material with which we want to print. Dual extruder 3D printers are also referred to as IDEX 3D printers.
Printing with HIPS requires a heated bed and should be done in a separate room due to the fumes. When not used as a support material, parts made with HIPS tend to be lightweight and rigid and may be easily sanded and painted.
Polyvinyl Alcohol (PVA)
PVA is to PLA what HIPS is to ABS, a dissolvable support material. In the case of PVA, however, it is dissolvable in warm water. PVA is very hygroscopic (meaning it absorbs moisture) and must be as dry as possible when printed with.
PVA requires a heated bed set to a temperature of around 60 degrees Celsius. PVA is printed with a nozzle temperature between 190 – 210 degrees Celsius. When used with dual extruder 3D printers, the extruder loaded with PVA should have its heater block turned off when not in use so as to avoid jamming.
Carbon fiber
Carbon fiber is used to lace other filament types, such as PLA, ABS, nylon, and PETG, to make them stronger. Prints made with a carbon fiber-laced filament can be made lighter due to this additional strength. It should be noted, however, that carbon fiber is abrasive to the nozzle on our extruder and thus a hardened steel nozzle is recommended when printing with carbon fiber-laced filaments. In Figure 1.20, we can see an arm for a quadcopter 3D printed with a carbon fiber-laced PETG filament:
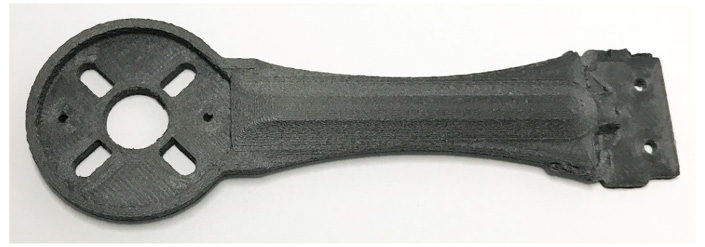
Figure 1.20 – Quadcopter arm
This part weighs just 8.5 grams and cannot be bent by hand.
Nylon
Nylon is one of the toughest plastics available. It is used in many products, such as zip ties. 3D printing with nylon can be challenging as it is a hygroscopic material and must be printed dry. Nylon prints are tough but slightly flexible. Figure 1.21 shows a 3D-printed nylon replacement buckle for a hockey helmet:
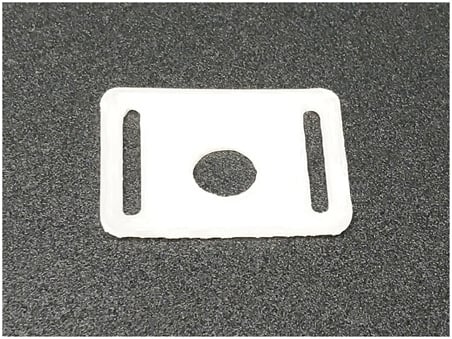
Figure 1.21 – 3D-printed buckle
The buckle flexes enough to be pushed over the metal button on the helmet.
Dry Boxes
Many materials used in 3D printing are very hygroscopic, meaning they absorb moisture from the air. This causes issues when printing as their diameters swell and jam up the extruder. A solution to this issue is to print from a dry box. A dry box is an airtight storage container with a small hole where filament is passed through and fed to the extruder on a 3D printer. Dry boxes may be purchased or easily made from existing airtight containers. There are also many DIY designs for dry boxes at places such as Thingiverse.com.
Flexible materials
Flexible filament can be used to print things such as phone cases and gaskets. In Figure 1.18, the part on the left was printed with a flexible material called NinjaFlex.
The term Thermoplastic Elastomer (TPE) is used to describe the blend of elastic and thermoplastic (soft rubber and hard plastic) that makes up the flexible material we 3D print with. Thermoplastic Polyurethane (TPU) is a common type of TPE that is more on the rigid side.
To better understand flexible filament and its uses, it is good to understand the Shore hardness scale. Comprising measurement devices (called durometers) calibrated at different strengths, there are three main scales: Shore OO, Shore A, and Shore D. In Figure 1.22, we can see the hardness of common non-metallic items:
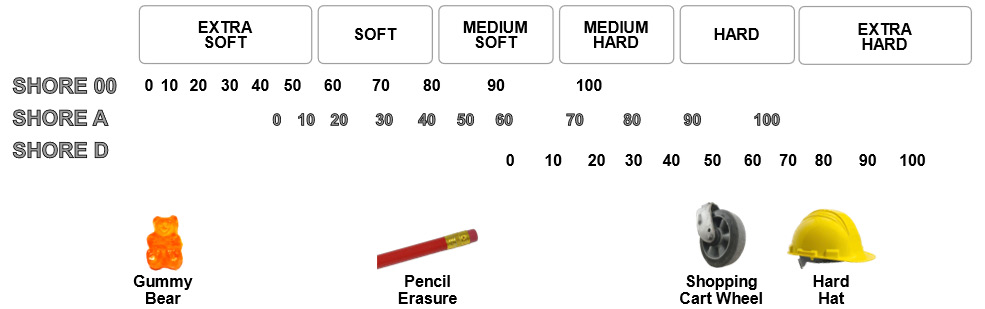
Figure 1.22 – Shore hardness scale
From Figure 1.22, we can see that a shopping cart wheel has a Shore hardness of 95A or 50D. The NinjaFlex used in Figure 1.18 has a hardness of 85A, meaning it is harder than a pencil eraser but softer than a shopping cart wheel.
Bowden tube extrusion systems tend to struggle at printing with flexible materials. Generally, a direct drive extrusion system is used to 3D print with flexible materials.
Other materials
Other materials available for 3D printing include wood-laced filaments, polycarbonate filaments, metal filaments, PolyEtherEtherKetone (PEEK) filaments, and so on. Many of the high-performance filaments require industrial 3D printers with heated chambers and could not be printed with an Ender 3 series printer.
As we can see, there are many materials available for use with 3D printing, and they are getting better and stronger all the time. In this book, we will work mainly with PLA and ABS.