Exploring the hallmarks of Lean Thinking
The goal of Lean is to maximize customer value, quality, and efficiency by minimizing waste and non-value-adding costs while optimizing delivery speed and throughput. The elimination of waste is the hallmark of Lean principles, as depicted in Figure 1.1:
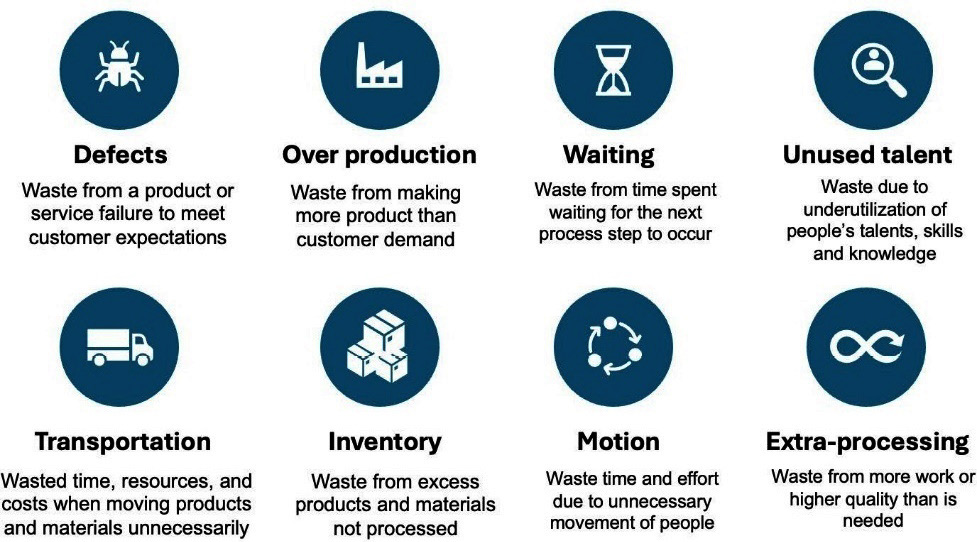
Figure 1.1 – Classic eight wastes of Lean
The essence of Lean is simple: organizations should refrain from investing in endeavors that produce excess work, features, or capabilities that customers neither desire nor find valuable. Failing to do so might drive external or internal customers to seek alternative products or services. The complexity lies in determining what customers need and the level of quality they anticipate while eliminating any elements that fail to align with their objectives. Lean practitioners refer to these excesses as waste.
A Lean enterprise’s imperative is continuously maximizing customer value at the lowest possible cost...