Understanding the levels of industrial automation
Industrial automation is a complex system with several devices communicating and working with each other to provide the desired result. The simplest way to describe the levels/hierarchy of industrial automation is by using a three-level representation, as shown here:
- Field level
- Control level
- Supervisory and production level
We will describe each of these levels in the following section and provide the relevant examples for ease of understanding.
Field level
This is the lowest level in the hierarchy of industrial automation. It consists of field devices such as sensors and actuators, which are used in industrial automation. Sensors convert physical characteristics into electrical signals (digital or analog). They are input devices and can be referred to as the eyes and ears of automation. Examples of sensors include proximity sensors, temperature sensors, pressure sensors, level sensors, flow sensors, and limit switches. Actuators, on the other hand, convert electrical signals (digital or analog output signals) into physical characteristics, which can be in the form of motion. Examples include AC/DC motors, servo motors, stepper motors, pumps, control valves, solenoids, contactors, and relays. The job of the field devices (sensors and actuators) is to transfer machine and process data to the next level (control level) for monitoring and analysis.
This level can be referred to as the eyes and arms (hands) of an industrial automation system. The sensor is acting as the eyes, while the actuator is acting as the arms. Real-time process parameters such as temperature, pressure, level, and flow are converted into electrical signals by the sensors. Data that's collected from the sensors is transferred to the controller for further monitoring and analysis. The actuators control the process parameter through a signal from the controller.
Control level
This level consists of programmable logic controllers (PLCs) or other forms of controllers. PLCs are the brains behind modern industrial automation. They are used to carry out control functions in industries. They take data from different kinds of sensors, make decisions using the program written into it, and output a control signal that the actuator will use to carry out the required task. They can be programmed to deliver automatic control functions based on the signals they receive from sensors. More details on PLCs will be provided in Chapter 7, Understanding PLC Hardware and Wiring, and Chapter 8, Understanding PLC Software and Programming with TIA Portal.
Supervisory and production level
This level consists of Supervisory Control And Data Acquisition (SCADA) and Human Machine Interface (HMI), among others, for monitoring and controlling various parameters and setting production targets. Chapter 10, Understanding Human Machine Interfaces (HMIs), explains HMI while Chapter 11, Exploring Supervisory Control And Data Acquisition (SCADA), explains SCADA.
To help you gain a better understanding of HMI and SCADA, this book has been arranged to cover some basic knowledge of industrial automation before venturing into HMI and SCADA.
The following diagram represents the basic levels of industrial automation:
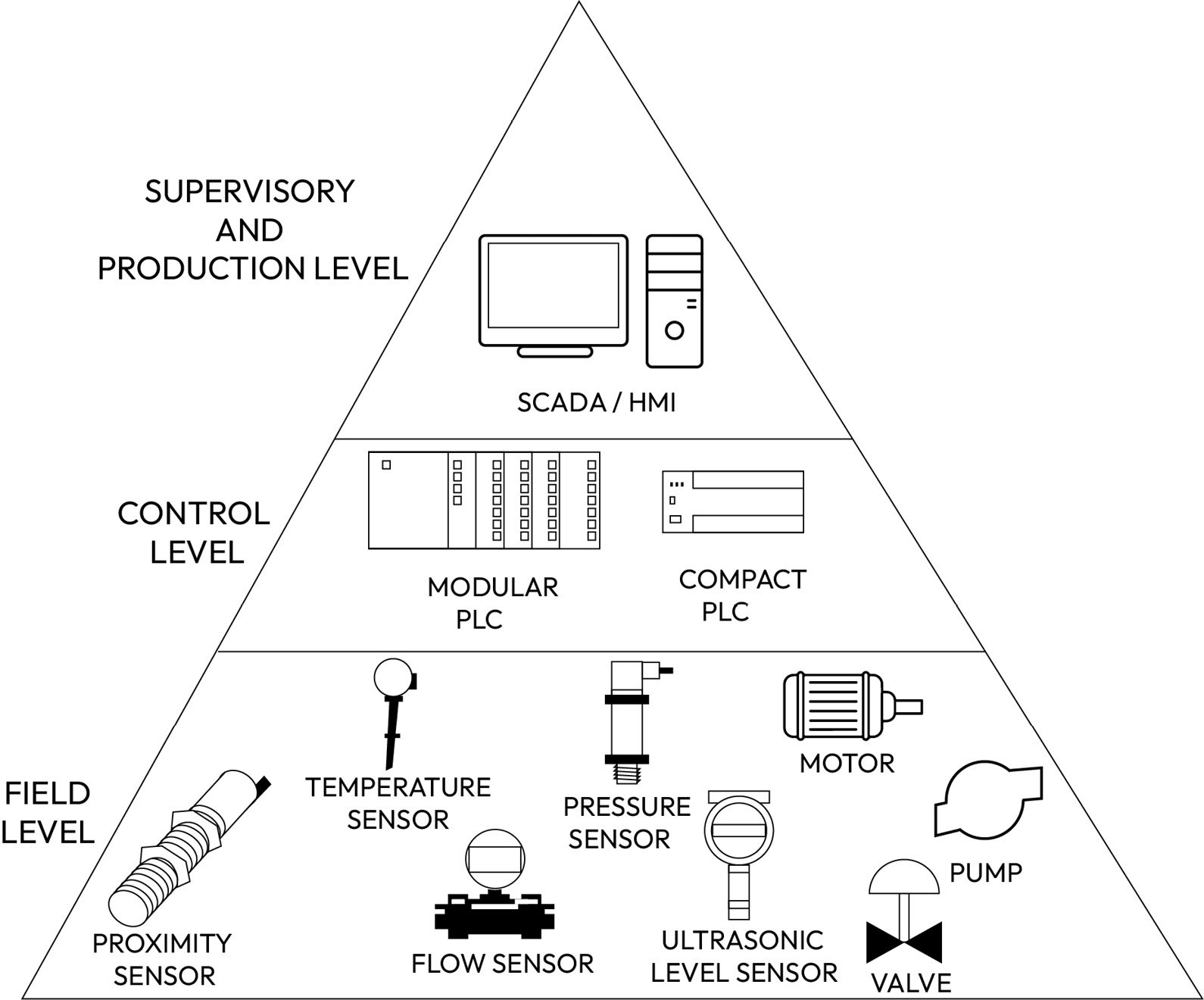
Figure 1.5 – Levels/hierarchy of industrial automation
In this section, you learned about the basic levels of industrial automation, which include the field level, the control level, and the supervisory and production level. Chapter 2, Switches and Sensors – Working Principles, Applications, and Wiring, and Chapter 3, Actuators and Their Applications in Industrial Automation, will give more detailed explanation on field level. Chapter 7, Understanding PLC Hardware and Wiring, Chapter 8, Understanding PLC Software and Programming Using the TIA Portal, and Chapter 9, Deep Dive into PLC Programming with TIA Portal, will give detailed explanation on the control level using hands-on approach while Chapter 11, Exploring Supervisory Control And Data Acquisition (SCADA), will further explain the supervisory and production level and include a hands-on project/practical project (interfacing SCADA with S7-1200 PLC using mySCADA software) that will give you a practical experience and understanding of the concept.