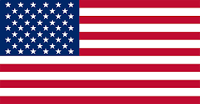
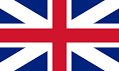
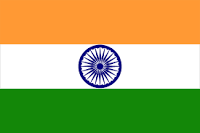
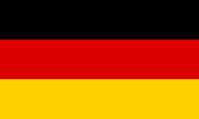
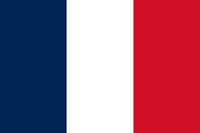
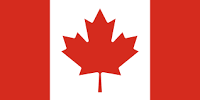
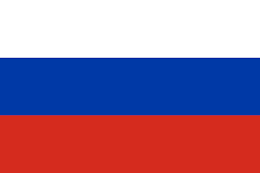
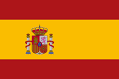
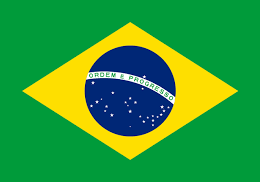
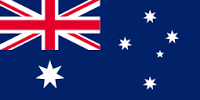

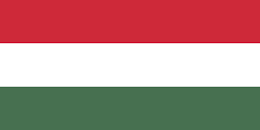
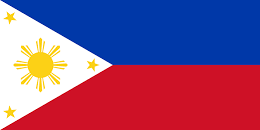
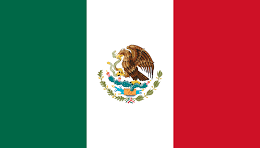
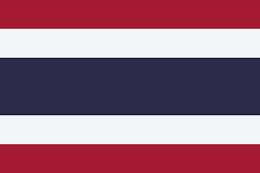
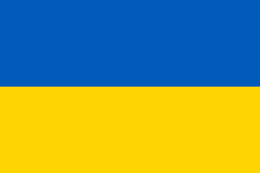
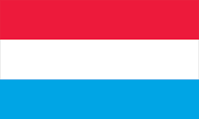
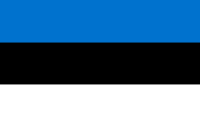
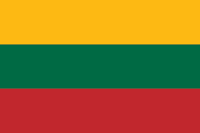
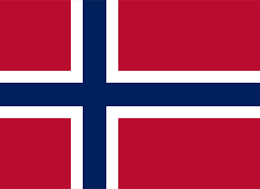
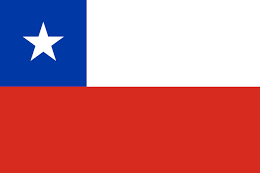
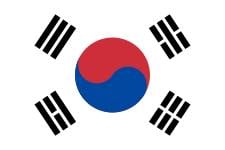
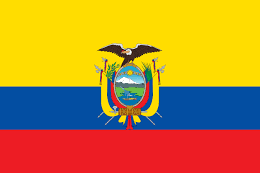
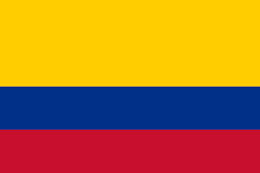
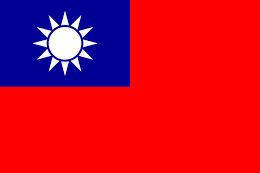
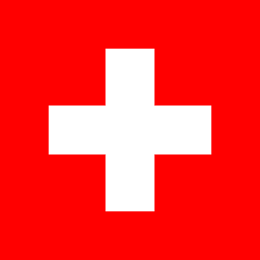
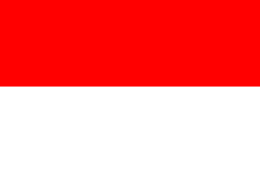
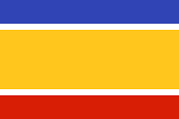
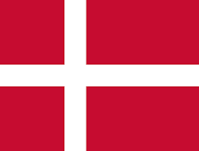

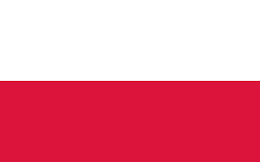
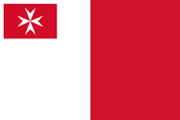
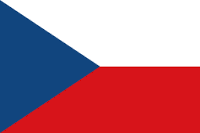
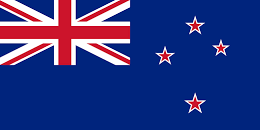
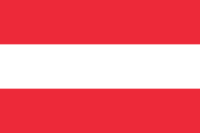
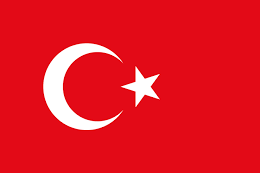
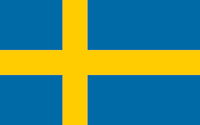
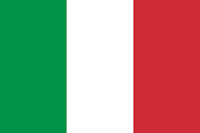
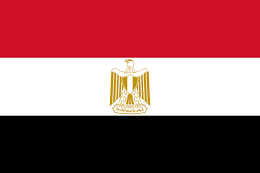
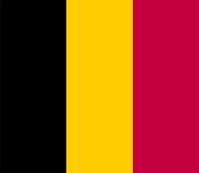
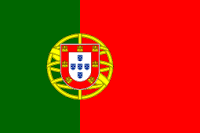
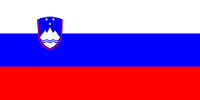
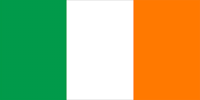
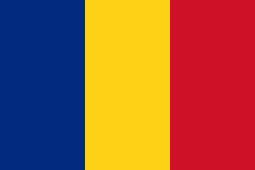
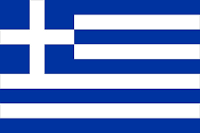
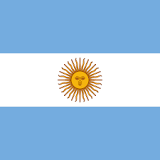
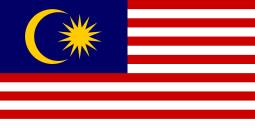
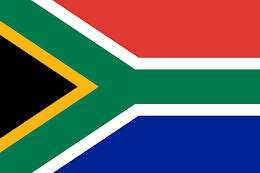
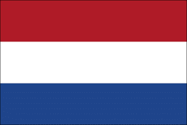
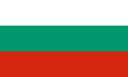
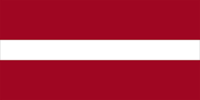
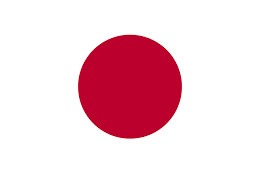
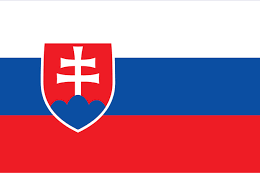
(For more resources related to this topic, see here.)
First, you will need to build an attachment to hold the color sensor onto the robot.
Insert an axle that is five modules long into the color sensor. Place bushings onto the axle on either side of the sensor. This is illustrated in the following figure:
Attach the two-pin one-axle cross blocks onto the axle outside the bushings. This is illustrated in the following figure:
Insert 3-module pins into the cross blocks as shown in the following figure:
The pins will attach to the robot just in front of the castor. The bottom of the color sensor should be approximately leveled with the plastic part of the castor holder. If you are on a flat hard surface, your light sensor will be half a centimeter above the ground. If you are on a soft surface, you may need to add a spacer to raise up the sensor. This is illustrated in the following figure:
We are going to write a proportional line following code similar to the code used for the ultrasonic motion sensor.
MotorBPower = Speed - Gain * (LightSensor - DesiredValue)
MotorCPower = Speed + Gain * (LightSensor - DesiredValue)
This algorithm will make corrections to the path of the robot based on how far off from the line the robot is. It determines this by calculating the difference between the light sensor reading and the value of the light sensor reading on the edge. Each wheel of the robot rotates at a different speed proportional to how far from the line it is. There is a base speed for each wheel and then they will go either slower or faster for a smooth turning. You will find that a large gain value will be needed for sharp turns, but the robot will tend to overcorrect and wobble when it is following a straight line. A smaller gain and higher speed can work effectively when the line is relatively straight or follows a gradual curve. The most important factor to determine is the desired light sensor value.
Although your color sensor can detect several colors, we will not be using that feature in this program. The color sensor included in your kit emits red light and we are measuring the reflection of that reflected light. The height of the sensor above the floor is critical, and there is a sweet spot for line tracking at about half a centimetre above the floor. The light comes out of the sensor in a cone. You want the light reflected into the sensor to be as bright as possible, so if your sensor is too high, the reflected intensity will be weaker. Assuming your color sensor is pointing straight down at the floor (as it is in our robot design), then you will see a circular red spot on the floor. Because the distance between the detector and the light emitter is about 5 to 6 mm, the diameter of this circle should be about 11 mm across. If the circle is large, then your color sensor is too high and the intensity will weaken. If the circle is smaller than this, then the sensor will not pick up the emitted light.
The color sensor in the LEGO MINDSTORMS EV3 kit is different from the optical sensors included in the earlier LEGO NXT kits. Depending on your application, you might want to pick up some of the older NXT lights and color sensors. The light sensor in the NXT 1.0 kit could not detect color and only measured reflected intensity of a red LED. What is good about this sensor is that it will actually work flush against the surface and saves the need to calibrate changes due to the ambient lighting conditions. The color sensor in the NXT 2.0 kit actually emitted colored lights and contained a general photo detector. However, it did not directly measure color, but measured the reflection of colored light, which it would emit. This actually allowed you to track along different colored lines, but it was also slower. The new EV3 sensor detects colors directly, works quickly, and emits only red light.
This article taught us to alter our robot, so it can track a line using an optical sensor. We used a proportional algorithm and adjusted the parameters for optimum tracking. Finally, we also wrote a program allowing the robot to be calibrated without the use of a computer.
Further resources on this subject: